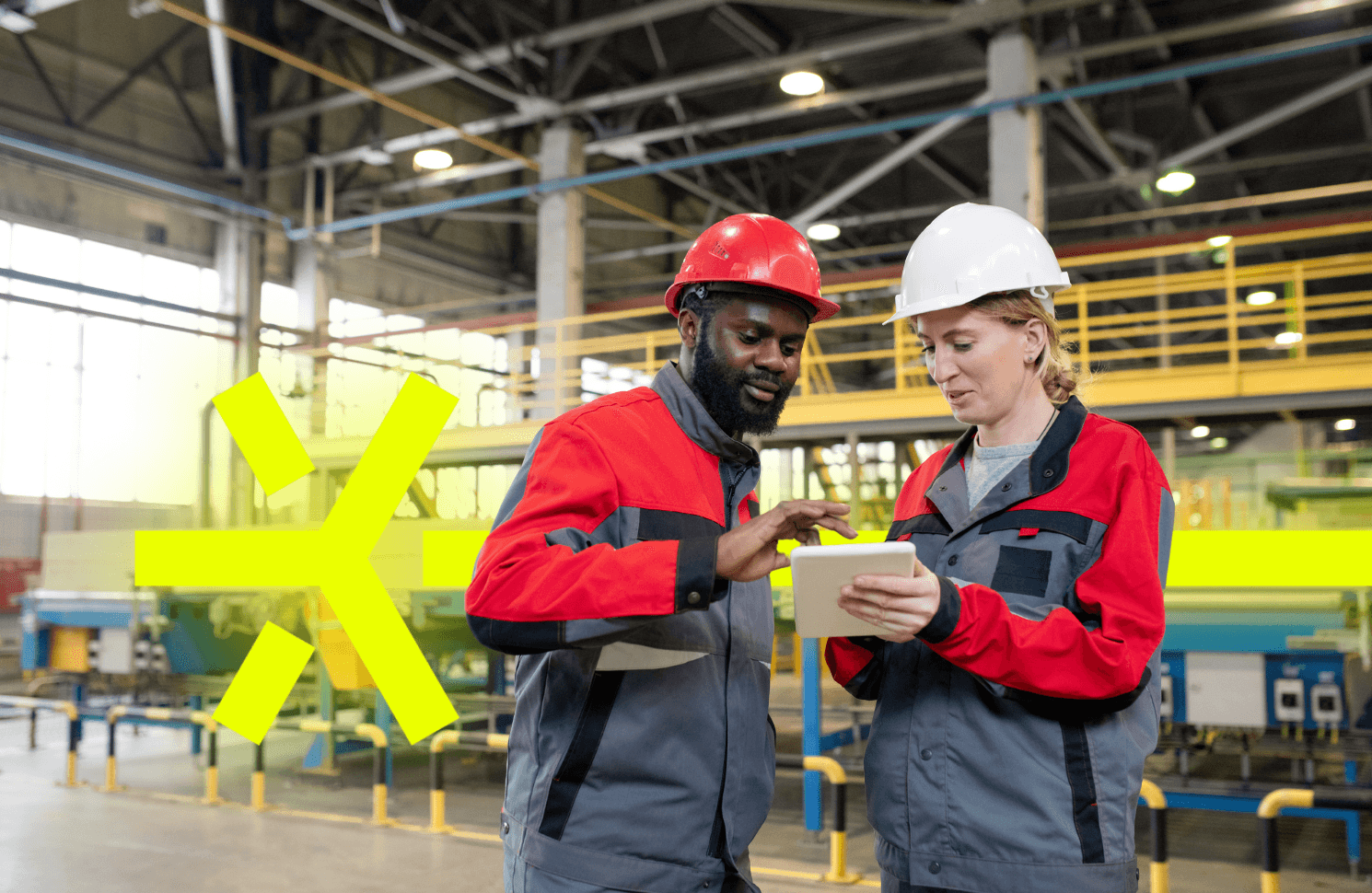
How CIOs can drive modern manufacturing with application innovation and AI
JUN. 20, 2025
4 Min Read
Your factory floor will no longer wait months for new software to prove its worth.
Modern cloud platforms, generative AI, and modular architectures now shrink deployment cycles from quarters to weeks. As a technology leader, you’re expected to convert those gains into higher throughput, lower scrap, and happier customers. Waiting for yesterday’s monolithic systems to catch up is not an option.
Teams that once focused solely on uptime are now stewards of data pipelines, machine learning models, and digital twins. You need clear priorities, predictable budgets, and predictable results. When application innovation meshes with artificial intelligence, the payoff arrives in hard metrics: cycle-time compression, higher first-pass yield, and double-digit cost savings. That value is why manufacturing modernization tops every board agenda this year.
key-takeaways
- 1. Manufacturing modernization must connect software flexibility to measurable production outcomes to justify executive investment.
- 2. Generative AI reduces time to value by enabling faster experimentation, root-cause analysis, and defect prevention without deep technical overhead.
- 3. Modular, containerized architectures allow modernization efforts to operate in parallel with existing systems, accelerating deployment and minimizing disruption.
- 4. CIOs and CTOs should prioritize unified data foundations, standardized security, and KPI-linked funding strategies to scale success.
- 5. Application modernization using generative AI allows manufacturing IT leaders to reduce operational costs, speed innovation cycles, and align outcomes to board-level goals.
Why manufacturing modernization requires application innovation and AI
Legacy manufacturing execution systems were built for stable product lines and incremental improvement, not high-mix production and instant analytics. They struggle with streaming sensor data, multi-plant orchestration, and the exploding variety of edge devices. Keeping those systems alive absorbs talent that could be writing microservices or scaling AI workloads. As the skills shortage bites, every hour spent on patches is an hour not spent on revenue growth.
Modern manufacturing and engineering demand cloud-native architectures that separate data, logic, and presentation. Containerized workloads allow you to push updates during scheduled downtimes without touching PLC code. When AI modules sit beside those workloads, anomaly detection, predictive maintenance, and adaptive process control shifts from pilot to production. This tight feedback loop turns raw data into frontline improvements that plant managers can trust.
"Waiting for yesterday’s monolithic systems to catch up is not an option."
How generative AI reduces time to value in modern manufacturing
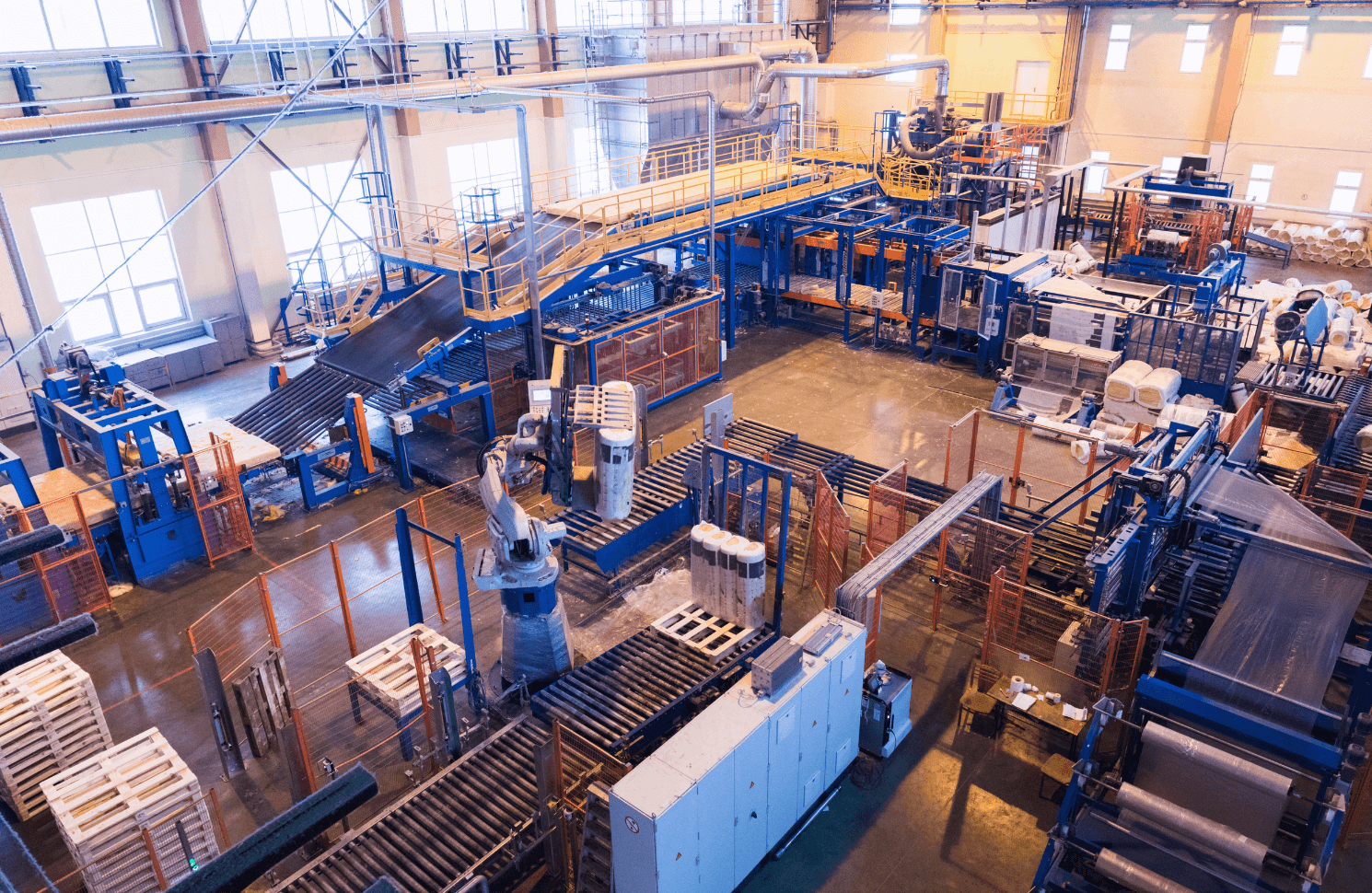
Traditional machine learning models depend on careful feature engineering, lengthy training cycles, and specialist oversight. Generative AI flips that timeline by pre-training on massive data sets, then fine-tuning with relatively small amounts of factory-specific data. Operators can describe a defect in plain language and receive suggested root-cause hypotheses in seconds. That conversational interface removes bottlenecks that once stalled Six Sigma projects for months.
Generative AI also accelerates design-for-manufacturability. Engineers feed initial CAD files into a model that proposes geometry tweaks for easier machining or additive builds. Simulation, iteration, and documentation unfold in days instead of quarters. Every shortened loop means faster first article approval, earlier market entry, and stronger margins.
Strategic benefits of application modernization for manufacturing leaders
You carry direct accountability for uptime, yield, and profitability. Updating outdated code bases is not just an IT chore; it is a profit lever. Modernization converts brittle systems into flexible service layers that respond to market shifts with minimal disruption. Clear financial impact and faster value capture earn board-level endorsement every quarter.
- Higher asset utilization: Microservices let you adjust line parameters without risking a full system reboot, which keeps machines cutting, welding, or printing at peak capacity. Continuous software delivery raises equipment availability by double digits while trimming unplanned downtime.
- Lower total cost of ownership: Moving to container orchestration eliminates expensive vendor lock-in and custom hardware. Cloud-based monitoring trims on-premise licensing fees and slashes upgrade labor.
- Faster product introduction: API-first design connects product lifecycle management (PLM) tools with execution systems, cutting engineering change order cycles from weeks to hours. Shorter changeovers support high-mix, low-volume strategies that command premium pricing.
- Improved quality analytics: Streaming data pipelines merge process, test, and warranty records into a single context store. Machine-vision models detect defects earlier, reducing scrap and warranty payouts.
- Consistent governance: Role-based access and policy-as-code enforce security without slowing operations. Regulatory updates roll out once and propagate across every plant, minimizing audit risk.
- Scalable innovation fund: Retired maintenance spend shifts toward proofs-of-value and pilots that drive cash flow. Clear KPIs around cost avoidance and revenue lift make budget discussions straightforward.
Modernization initiatives pay off only when they tie software flexibility to measurable production gains. Leaders who link microservice roadmaps to plant scorecards see adoption soar. Transparent ROI builds internal champions across operations, engineering, and finance. Your peers already treat modernization as a business strategy instead of a technology upgrade.
The role of application modernization using generative AI for manufacturing
Combining service-oriented architecture with generative AI creates a virtuous cycle. Modular applications feed curated data into large models, while those models surface new insights that justify more modularity. Each improvement funds the next sprint, keeping momentum high. You end up with a self-reinforcing system that never grows stale.
Data unification for faster insights
Centralizing heterogeneous data sources once required months of extract-transform-load scripting. Now, vector databases align sensor streams, maintenance logs, and supplier records in standard embeddings within days. That unified layer fuels language models that answer production questions in seconds. When shop-floor teams trust the data, adoption follows naturally.
Data quality matters just as much as model power. Automated lineage tracking flags stale or corrupt feeds before they skew metrics. Governance workflows approve changes without extra manual steps. Clear provenance turns AI recommendations into actionable instructions.
Autonomous quality control loops
Vision models generate synthetic defect examples to balance skewed training sets. That trick raises detection accuracy for rare failure modes without extra data collection. Within the container orchestration layer, new weights roll out during lull periods with no manual tuning. Scrap reduction shows up on the next daily production meeting report.
Closed-loop quality control pairs detection with adaptive process adjustments. If the model spots a drift in paint thickness, a microservice triggers a line-speed tweak while logging the action for traceability. Over time, the model learns the most effective countermeasures. Quality engineers then focus on preventative policies instead of firefighting.
Predictive supply chain coordination
Large language models summarize supplier risk signals pulled from logistics feeds, purchase orders, and public news. Planners receive concise mitigation options long before material shortages threaten line stoppage. That foresight keeps finished-goods commitments intact, protecting revenue.
Context-aware prompts tie supply signals to machine schedules, highlighting swap-in alternatives and recalculated takt times. Automated what-if analysis anchors sourcing meetings in concrete line-level implications. Staff spend less time downloading spreadsheets and more time approving profitable substitutions.
Human-machine collaboration at scale
Generative copilots translate maintenance procedures into multiple languages, visual step-by-step guides, and augmented-reality overlays. Technicians scan a QR code on the asset tag and receive contextual instructions tailored to the specific serial number. Standard work variance falls, and onboarding time for new hires drops.
On the engineering side, conversational interfaces sit atop simulation engines. Designers articulate constraints in natural language, and the system proposes parameter sweeps with cost estimates. Decisions become transparent and auditable, accelerating sign-off across departments.
Continuous compliance and security
Regulations such as ISO 21434 or ITAR evolve frequently and leave little room for delay. Policy-as-code repositories push rule updates directly into deployment pipelines, blocking non-compliant builds at compile time. Large models read the same policies and generate remediation steps with citations to the clause level.
Security teams integrate anomaly detectors that model both network traffic and user behavior. Unusual equipment commands trigger multi-factor prompts before execution, protecting physical assets. That built-in vigilance satisfies auditors and reduces insurance premiums.
Application modernization using generative AI for manufacturing gives you a stack that learns, adapts, and scales. It turns every byte of production data into a line-item improvement in your P&L. Leadership teams appreciate a roadmap where innovation funds itself through continuous savings. Stakeholders embrace progress when results arrive without disruption.
Use cases for generative AI in modern manufacturing and engineering
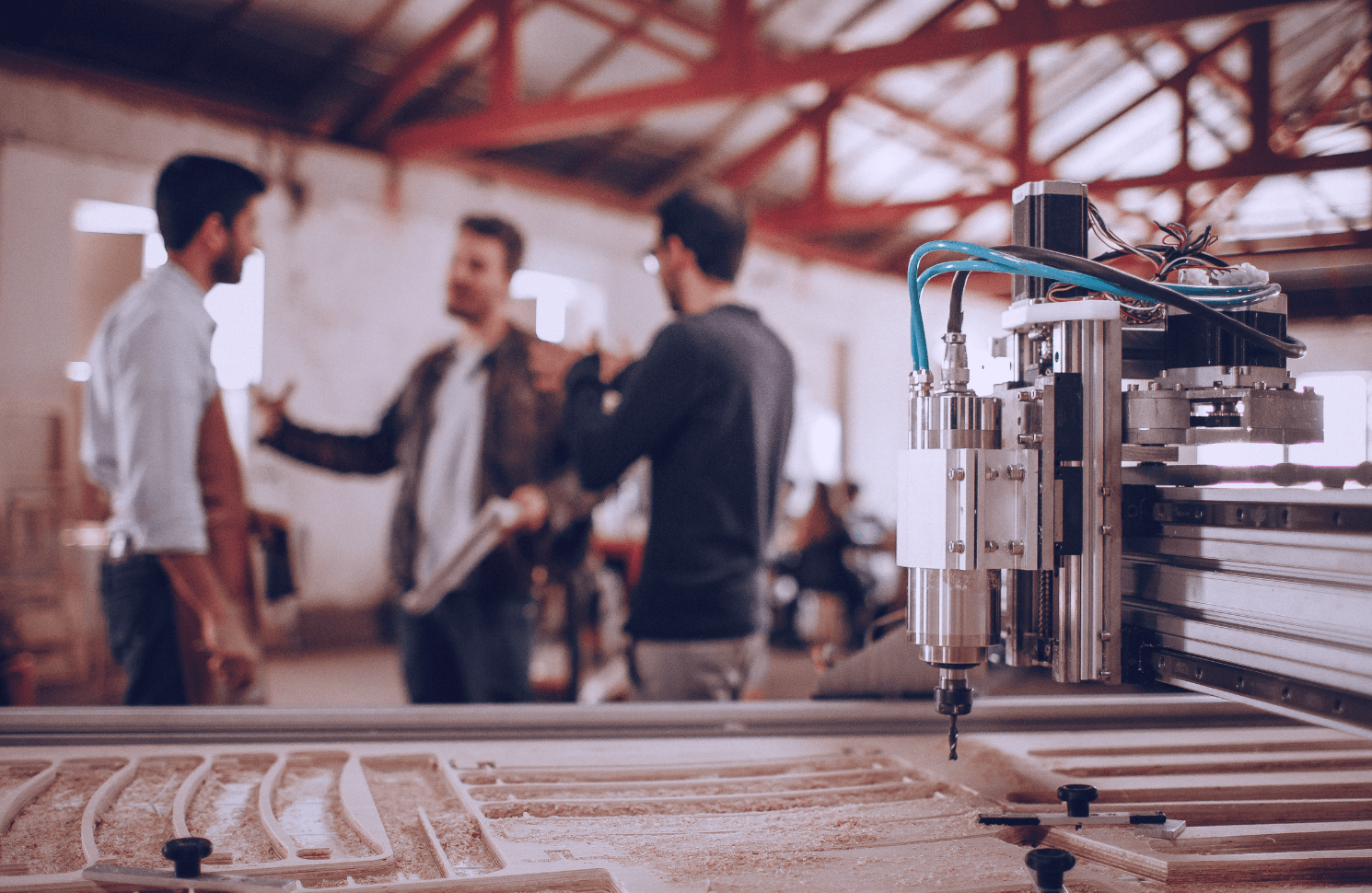
Plain-language interfaces have removed many barriers between shop-floor know-how and advanced analytics. When workers talk to machines instead of coding them, ideas proliferate. Product engineers and operators collaborate without translation gaps, shortening the path from insight to action. Costs fall, safety improves, and customers notice the difference.
- Process-step optimization: Generative models suggest CNC toolpaths or welding sequences that cut cycle time while preserving tolerance, then document the change for ISO compliance.
- Work-instruction generation: AI converts BOM and routings into operator-specific guides with images and short videos, improving first-time build accuracy.
- Virtual equipment commissioning: Digital twins seeded with generative AI predict line behavior before hardware arrives, letting you pre-tune control loops and shave weeks off start-up.
- Energy-load balancing: Models synthesize historic consumption patterns, spot inefficiencies, and propose rescheduling heavy loads outside peak pricing windows.
- Predictive workforce scheduling: AI aligns shift assignments with skill requirements, anticipated demand spikes, and overtime constraints, boosting morale and reducing turnover.
- Design variant exploration: Engineers prompt the model with cost, weight, and sustainability targets, receiving dozens of manufacturable design alternatives for quick screening.
These use cases prove that generative AI is not a lab curiosity. Each one maps directly to throughput, cost, or customer success metrics. When value shows up on financial statements, funding for the next pilot arrives without friction. Your responsibility is to prioritize the sequence that yields the fastest payback.
What CIOs and CTOs need to prioritize when planning for manufacturing modernization
Strategy without execution leaves money on the table. You’re judged on results, not intentions. Picking the right focus areas at the outset shortens payback, builds credibility, and frees budget for future sprints. The priorities below come from field-tested programs across multiple plants.
Align funding with business outcomes
Technology roadmaps must anchor every line item to EBITDA impact. When finance sees numbers tied to throughput or reduced warranty claims, approvals move swiftly. Avoid vanity metrics and focus on cash-flow improvement within the fiscal year. Clear alignment eliminates second-guessing during steering committee reviews.
Cross-functional steering groups maintain momentum once funding lands. They meet weekly and approve scope changes based on agreed KPIs. Transparent dashboards show progress in near real time. Stakeholders stay engaged because results remain visible.
Standardize data foundations early
Disparate schema slows every project that follows, so lock down naming conventions and governance policies first. Adopt a common data model that spans quality, maintenance, and supply functions. Consistency reduces integration rework and avoids endless debates over “single source of truth” definitions. Faster integrations translate into quicker wins.
Streaming architecture brings incremental adoption while preserving existing historians. Edge gateways publish MQTT topics that feed central lakes without heavy lifts. Data scientists get reliable sources, and plant teams keep local visibility. Everybody wins time.
Invest in scalable security
Cyber incidents shut down production and erode trust. Zero-trust principles applied to OT keep threats confined while allowing legitimate traffic. Token-based authentication and micro-segmentation protect both new microservices and older control networks. Insurance premiums drop once auditors verify controls.
Security gets easier when pipelines enforce compliance. Code commits trigger automated scans for vulnerabilities, license issues, and misconfigurations. Problems surface before deployment, making fixes cheaper. A secure foundation supports every other modernization goal.
Build a modular talent strategy
Software, data, and machine learning talent seldom reside in one department. Rotational programs give engineers exposure to Python, MLOps, and cloud orchestration without gutting operations headcount. External partners cover gaps while internal teams build new skills. Retention improves when staff see a clear growth path.
Vendor contracts should include knowledge-transfer milestones. Workshops, paired programming, and documentation walkthroughs create self-sufficiency. Over time, external spend shifts from hands-on delivery to strategic advisory. Your bench grows stronger each quarter.
Measure and broadcast progress
Weekly scorecards tie technical metrics, such as deployment frequency, to business metrics such as on-time delivery. Celebrating even small victories sustains enthusiasm across departments. Transparent reporting prevents scope creep and maintains alignment with board expectations. Momentum converts skeptics into sponsors.
Mid-project course corrections rely on those same dashboards. Leading indicators such as defect density or pipeline wait time predict risk before milestones slip. Teams act early and avoid costly rework. Predictability breeds confidence.
Prioritization is the hallmark of mastery in modern advanced manufacturing. When each initiative traces a straight line to profit, support flows from every executive channel. Clear data foundations and secure pipelines keep surprises at bay. A repeatable operating rhythm ensures gains compound quarter after quarter.
"Streaming architecture brings incremental adoption while preserving existing historians."
Key challenges CIOs face in modern advanced manufacturing today
Ambitious roadmaps bump into harsh realities on the plant floor. Digital initiatives often stall because practical obstacles outweigh strategic intent. Identifying these hurdles early lets you allocate mitigation budgets instead of firefighting later. Knowing the pitfalls arms you for faster execution.
- Technical debt overload: Decades-old PLC ladders and proprietary HMIs slow every integration effort, draining budgets before new value starts flowing.
- Fragmented data ownership: Quality, maintenance, and supply teams use disconnected systems, leading to redundant storage and conflicting metrics that derail analytics.
- Skill scarcity: Full-stack developers, data engineers, and control specialists remain hard to recruit, and retention suffers when projects pause for approvals.
- Change fatigue: Operators and supervisors already juggle Lean, Six Sigma, and regulatory audits; another initiative without clear benefits, risks, or pushback.
- Cyber exposure: Converged IT-OT networks expand attack surfaces far beyond traditional firewalls, making outage avoidance a daily concern.
- Supplier reliability: Just-in-time inventory magnifies the impact of even minor parts delays, forcing line stoppages that erode quarterly targets.
Each challenge carries a cost in lost output, inflated spend, or missed deadlines. Leaders who confront them head-on position their plants for sustained gains. Proactive risk management keeps executive sponsors confident and funding reliable. Address hurdles early and watch modernization momentum accelerate.
How Lumenalta helps you accelerate modern manufacturing with AI innovation
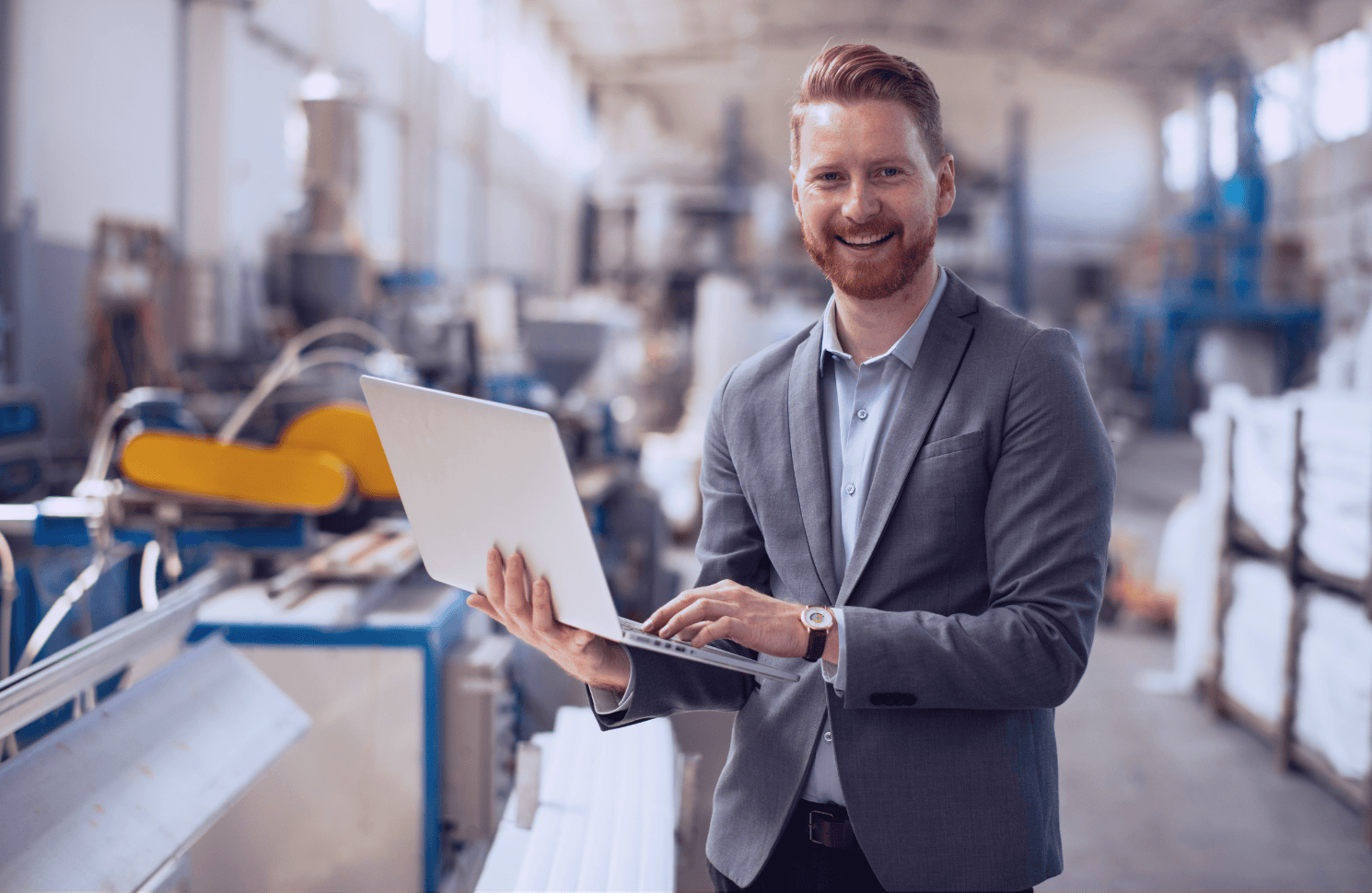
Your peers expect measurable gains, not slideware. Lumenalta’s co-creation model places our architects side by side with your plant engineers to deliver weekly software drops that connect cloud, edge, and AI workloads. Our microservice accelerators cut code scaffolding by half, allowing your developers to focus on value-adding logic. Proven reference architectures integrate seamlessly with your existing control systems, so production never pauses for upgrades.
Persistent data pipelines feed our reference generative models, letting your teams ask plain-language questions about yield, scrap, and cycle time. Security controls and governance templates satisfy ISO and ITAR auditors without slowing iteration. Cost-of-ownership dashboards translate technical metrics into finance-ready reports, proving ROI every sprint. Your board sees hard numbers, your staff sees fewer headaches, and you see progress that sticks.
Our engagement never ends at the hand-off. We coach your personnel on MLOps, cloud operations, and secure coding so skills remain long after the project closes. Quarterly value-realization reviews keep roadmaps aligned with business goals, ensuring continuous payoff. You gain a strategic ally committed to measurable outcomes, not a vendor chasing change orders. Trust Lumenalta to turn AI-powered modernization into sustained advantage.
table-of-contents
- Why manufacturing modernization requires application innovation and AI
- How generative AI reduces time to value in modern manufacturing
- Strategic benefits of application modernization for manufacturing leaders
- The role of application modernization using generative AI for manufacturing
- Use cases for generative AI in modern manufacturing and engineering
- What CIOs and CTOs need to prioritize when planning for manufacturing modernization
- Key challenges CIOs face in modern advanced manufacturing today
- How Lumenalta helps you accelerate modern manufacturing with AI innovation
- Common questions about modern manufacturing
Common questions about modern manufacturing
What’s the most effective way to start modernizing my manufacturing systems with AI?
How do I justify AI investment in manufacturing to my board or CFO?
Can generative AI really work with my existing OT and legacy systems?
Where should CIOs focus first when modernizing applications in advanced manufacturing?
How do I scale AI initiatives across multiple manufacturing sites?
Want to learn how modern manufacturing can bring more transparency and trust to your operations?