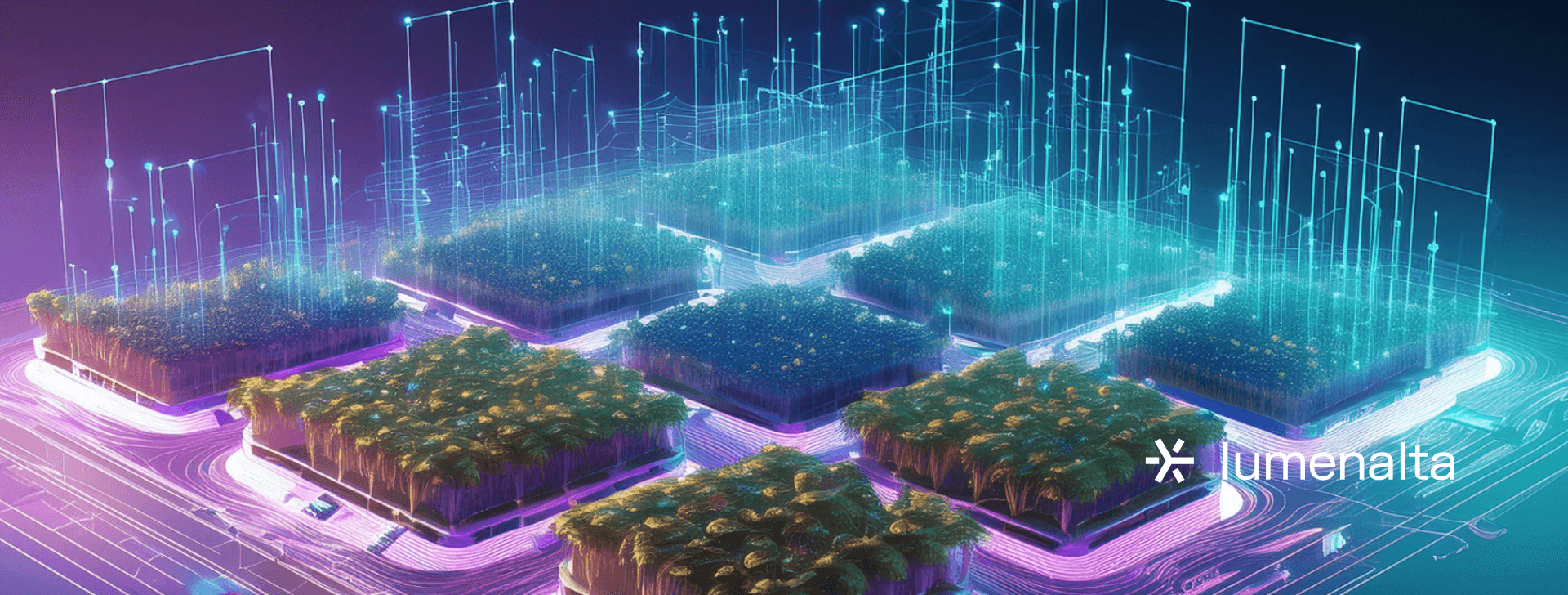
7 computer vision applications in manufacturing
JAN. 12, 2025
6 Min Read
Computer vision is reshaping the manufacturing industry by automating complex tasks, improving efficiency, and driving measurable results.
This advanced technology uses AI-powered image processing to analyze production lines, detect anomalies, and deliver actionable insights. By addressing critical challenges like quality control, maintenance, and safety, computer vision offers manufacturers new ways to optimize operations and maximize returns.
Key takeaways
- 1. Computer vision improves manufacturing processes by automating quality inspections, enhancing safety, and optimizing assembly tasks.
- 2. Predictive maintenance powered by computer vision helps reduce downtime, improve equipment lifespan, and control repair costs.
- 3. Integrating computer vision requires overcoming challenges like initial investment, system compatibility, and workforce readiness.
- 4. Computer vision applications extend beyond production lines to supply chain optimization and packaging verification.
- 5. Addressing operational inefficiencies and delivering actionable insights let computer vision allow manufacturers to achieve faster time-to-market and better scalability.
What is computer vision in manufacturing?
Computer vision in manufacturing uses artificial intelligence (AI) and image processing to analyze visual data captured from cameras and sensors on production lines. Through advanced algorithms, it identifies patterns, detects anomalies, and processes visual information, allowing manufacturing facilities to automate tasks traditionally reliant on human observation.
This technology reshapes how businesses manage operations by improving precision, reducing errors, and optimizing workflows. From enhancing product quality to improving safety and efficiency, computer vision applications in manufacturing address critical operational challenges and help organizations achieve measurable improvements across their processes.
"Using automated quality inspection reduces waste, lowers rework costs, and improves overall product consistency."
Benefits of computer vision in manufacturing industry
Adopting computer vision for manufacturing creates significant opportunities for businesses to enhance productivity, improve quality, and reduce operational inefficiencies. With production processes becoming complex, traditional methods often fail to meet the precision and scalability requirements of modern manufacturing. Computer vision technology addresses these challenges by automating labor-intensive tasks, analyzing visual data in real time, and optimizing workflows. It offers measurable improvements directly impacting business outcomes, including cost savings, faster production cycles, and improved resource utilization.
- Improved quality control: Automated vision systems detect defects and inconsistencies with unmatched precision, minimizing errors and maintaining high product quality.
- Increased production efficiency: Real-time monitoring and automated inspections streamline production processes, reducing delays and accelerating throughput.
- Reduced operational costs: By automating repetitive tasks and improving defect detection, businesses save on labor costs, material waste, and rework expenses.
- Enhanced workforce safety: Continuous visual monitoring helps manufacturers maintain safety compliance and identify risks, reducing workplace injuries and hazards.
- Predictive maintenance capabilities: Machine performance is monitored with advanced algorithms that anticipate failures, reducing costly downtime and prolonging equipment lifespan.
- Scalable operations: Computer vision adapts to different production scales, making it a cost-effective solution for businesses of all sizes.
- Actionable data insights: Analyzing visual data helps manufacturers refine processes, identify inefficiencies, and optimize resource allocation for better results.
The benefits of computer vision manufacturing go beyond operational improvements. They help businesses unlock untapped potential, deliver measurable results, and remain prepared for developing market needs. With this technology, organizations can achieve greater efficiency, reduced costs, and faster time-to-market, all while maintaining consistent product quality.
7 computer vision applications in manufacturing
Computer vision in manufacturing addresses critical business challenges by automating manual processes, improving operational accuracy, and delivering measurable improvements across production lines. As manufacturers seek to increase efficiency, reduce costs, and maintain high-quality standards, this technology provides solutions tailored to these needs. With computer vision use cases in manufacturing spanning defect detection, predictive maintenance, and product development, computer vision optimizes workflows while helping businesses achieve better time-to-market and long-term scalability.
1. Quality inspection and defect detection
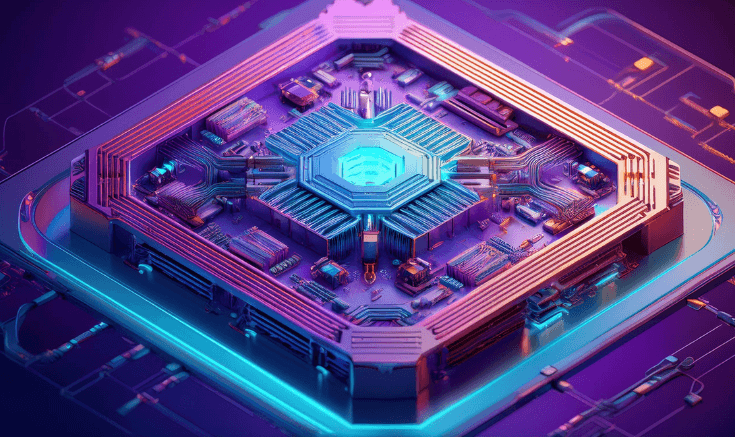
Manual inspection often falls short when it comes to detecting subtle or complex defects at high production speeds. Computer vision systems use advanced imaging technology and AI-driven algorithms to identify defects such as surface scratches, cracks, misalignments, and material inconsistencies. These systems provide a faster, more accurate alternative to traditional inspection methods. For example, in electronics manufacturing, computer vision ensures that solder joints are properly aligned and free of imperfections. In the food industry, it verifies that packaging meets hygiene and safety standards while identifying contamination risks.
Automated inspection reduces the likelihood of defective products reaching the customer, which in turn protects the company’s reputation and minimizes the cost of rework or recalls. The consistency of these systems also supports compliance with strict industry regulations, particularly in sectors such as automotive, aerospace, and pharmaceuticals. By analyzing defect trends over time, manufacturers can make process adjustments that improve production quality at scale.
2. Equipment monitoring and predictive maintenance
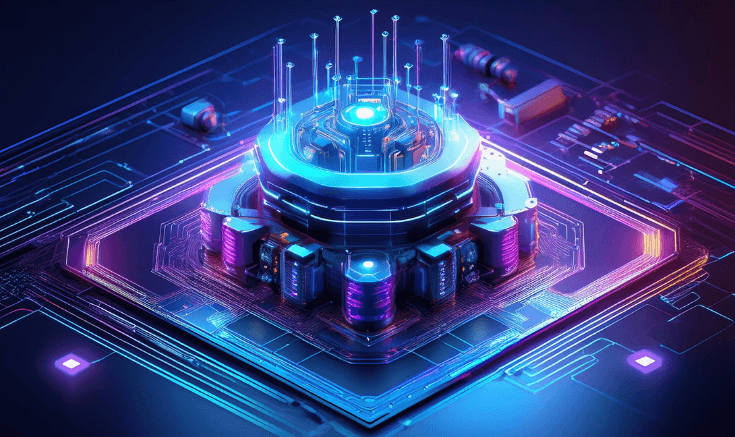
Unexpected equipment breakdowns can disrupt operations and lead to unplanned downtime, increased repair costs, and missed production deadlines. Computer vision systems analyze visual data to detect signs of wear and tear, misalignment, or overheating in machinery. For example, thermal imaging cameras integrated with AI detect small temperature variations in conveyor belts or motors, flagging potential failures before they happen. In precision manufacturing, high-resolution cameras monitor tool conditions during machining to prevent defects caused by dull or damaged tools.
Using this approach, manufacturers schedule maintenance proactively, avoiding costly disruptions. Predictive maintenance extends equipment lifespans, reduces repair expenses, and helps businesses maintain optimal production efficiency. The insights gathered from these systems also allow companies to adjust operational schedules and plan maintenance activities with minimal impact on productivity.
3. Workforce safety and compliance monitoring
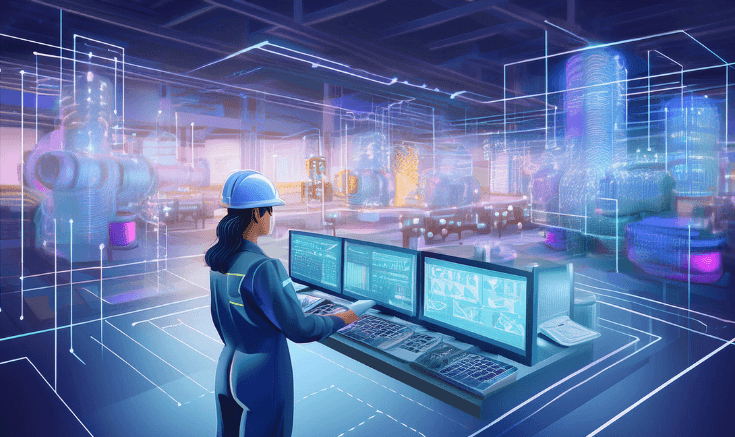
Ensuring worker safety is a top priority for manufacturers, especially in environments with heavy machinery, hazardous materials, or strict safety regulations. Computer vision systems actively monitor workplace conditions and identify safety risks in real time. For example, vision-based systems detect whether employees are wearing required personal protective equipment (PPE), such as helmets, gloves, or safety goggles. Cameras can also monitor restricted areas to ensure only authorized personnel are present or detect unsafe actions such as improper handling of equipment.
Immediate alerts enable supervisors to address risks as they arise, reducing the likelihood of accidents. Over time, the data collected from these systems supports improvements in safety protocols and training programs, creating a culture of accountability and reducing liability risks. Safer work environments contribute to higher employee morale and productivity while helping businesses meet regulatory compliance standards.
4. Automated product assembly
Manual assembly processes often struggle to meet the demands of high-speed production lines or the precision requirements of advanced industries. Computer vision enhances automated assembly systems by guiding robotic arms and ensuring accuracy during complex tasks. In the automotive industry, vision-guided robots assemble engines and other intricate components with unmatched precision. In electronics manufacturing, systems align tiny components on circuit boards, ensuring every element is positioned correctly before soldering.
Automated assembly reduces production errors, minimizes labor costs, and increases throughput, helping manufacturers meet high production demands without compromising quality. Additionally, manufacturers can scale operations more easily, reallocating human resources to higher-value tasks that require creativity or problem-solving.
5. Optimizing supply chains and logistics
Disruptions in supply chains can lead to inventory shortages, delivery delays, and missed revenue opportunities. Computer vision systems improve supply chain visibility and accuracy through real-time tracking, automated inventory management, and damage detection.
Imaging systems scan barcodes and QR codes to verify shipment contents and ensure accurate labeling. Cameras equipped with AI identify damaged goods during transit, allowing companies to address issues before products reach customers. Additionally, computer vision tracks inventory levels across warehouses, supporting better stock management and replenishment planning.
These capabilities allow manufacturers to streamline logistics operations, reduce costs, and meet delivery schedules more reliably. With more efficient supply chains, businesses respond quickly to changing customer needs, reducing delays and enhancing customer satisfaction.
6. Packaging accuracy and standards
Packaging errors, such as incorrect labeling, incomplete seals, or missing barcodes, can result in product recalls, fines, and customer dissatisfaction. Computer vision ensures packaging meets high standards through real-time inspection at various stages of the production line. For instance, systems check for proper alignment of labels, verify barcodes for accuracy, and inspect seals to confirm that products are securely packaged. In industries like food and beverage, computer vision identifies packaging defects that could compromise freshness or safety.
Automated inspection improves the consistency and efficiency of packaging processes, reducing waste and preventing defective items from leaving the facility. These systems protect brand reputation while ensuring compliance with industry regulations, which is particularly critical in regulated sectors like healthcare and pharmaceuticals.
7. Product design and prototyping
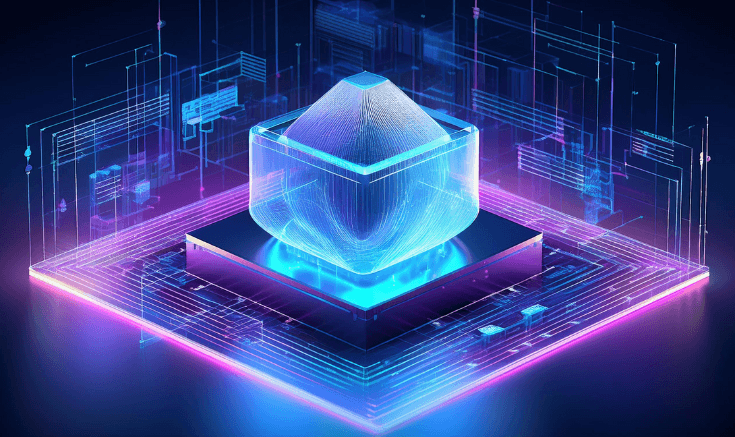
Product development often involves iterative design and testing, which can be time-intensive and prone to material waste. Computer vision accelerates this process by analyzing 3D models, prototypes, and materials for flaws or inefficiencies early in the development cycle. High-resolution imaging systems identify structural weaknesses in prototypes or pinpoint areas where materials can be optimized. In additive manufacturing, computer vision monitors 3D printing processes to ensure accuracy and detect errors such as layer misalignment or voids.
Shortening design cycles reduces time-to-market, allowing manufacturers to adapt quickly to customer demands or changing market conditions. Additionally, fewer material and process errors result in lower development costs and higher-quality final products.
Computer vision applications in manufacturing offer a comprehensive suite of tools to improve quality, safety, and efficiency across production lines. These solutions address immediate operational needs and position businesses for long-term growth and scalability, creating measurable business value while meeting varied industry requirements.
"Predictive maintenance enables manufacturers to address potential issues before they escalate into costly breakdowns."
Challenges in implementing computer vision in manufacturing
Computer vision technology offers unmatched opportunities to improve manufacturing efficiency, quality, and scalability. However, adopting this advanced technology often comes with challenges that businesses must carefully manage. These challenges stem from the technical complexities of implementation and the organizational adjustments required to integrate computer vision into existing systems. Addressing these barriers is essential to achieving measurable business impact and realizing the long-term value of this innovation.
- High initial investment: The costs associated with computer vision deployment can be substantial, including expenses for cameras, sensors, processing hardware, and software solutions. For smaller manufacturers or those operating with tight budgets, securing the capital needed to implement these systems can be a significant obstacle.
- Integration with legacy systems: Many manufacturing facilities still rely on older technologies that may not align easily with computer vision solutions. Establishing compatibility between modern systems and existing infrastructure often requires time, expertise, and financial investment.
- Data collection and quality challenges: Training effective computer vision algorithms depends on having access to high-quality and well-labeled data. Acquiring this data, cleaning it, and preparing it for use in machine learning models can be labor-intensive, requiring specialized skills and careful attention to detail.
- Workforce expertise gaps: Successful implementation and operation of computer vision systems require a workforce skilled in AI, machine learning, and system integration. Many manufacturers lack in-house expertise and must rely on external consultants or invest in upskilling their teams to meet these requirements.
- Cybersecurity risks: As computer vision systems involve connected devices and networks, protecting sensitive data becomes a priority. Manufacturers may face security vulnerabilities that could disrupt operations or expose proprietary information without proper safeguards.
- Inconsistent production conditions: Factory floors are often subject to variable conditions such as inconsistent lighting, vibrations from machinery, or differences in product appearance. These factors can affect the accuracy and reliability of computer vision systems, necessitating additional adjustments and optimizations.
- Resistance to change: Introducing advanced technologies can create resistance among employees and management. Concerns about potential disruptions, the learning curve for new systems, and fears of job displacement may hinder adoption efforts. Building trust and aligning stakeholders is critical to overcoming this challenge.
Although these challenges may seem daunting, they are not insurmountable. A strategic approach to implementation—supported by clear objectives, adequate resources, and strong collaboration between teams—can address technical and organizational barriers. Businesses that invest in overcoming these obstacles are rewarded with systems that improve operational efficiency, reduce costs, and unlock untapped growth opportunities—successfully integrating computer vision in manufacturing positions organizations to achieve measurable improvements while maintaining resilience in an aggressive market.
Computer vision is more than an innovation—it catalyzes brighter, faster, and more efficient manufacturing processes. From improving quality control to streamlining production workflows, this technology empowers businesses to unlock untapped potential and deliver measurable results. At Lumenalta, we specialize in creating tailored technology solutions that align with your business objectives, ensuring you stay ahead in an ever-growing market. Let’s build a brighter future together.
Table of contents
- What is computer vision in manufacturing?
- Benefits of computer vision in manufacturing industry
- 7 computer vision applications in manufacturing
- 1. Quality inspection and defect detection
- 2. Equipment monitoring and predictive maintenance
- 3. Workforce safety and compliance monitoring
- 4. Automated product assembly
- 5. Optimizing supply chains and logistics
- 6. Packaging accuracy and standards
- 7. Product design and prototyping
- Challenges in implementing computer vision in manufacturing
- Common questions about computer vision
Common questions about computer vision in manufacturing
What is computer vision in manufacturing used for?
How does computer vision improve manufacturing quality?
What industries benefit the most from computer vision in manufacturing?
What are the challenges of implementing computer vision?
What role does AI play in computer vision systems for manufacturing?
Want to learn how computer vision can bring more transparency and trust to your operations?