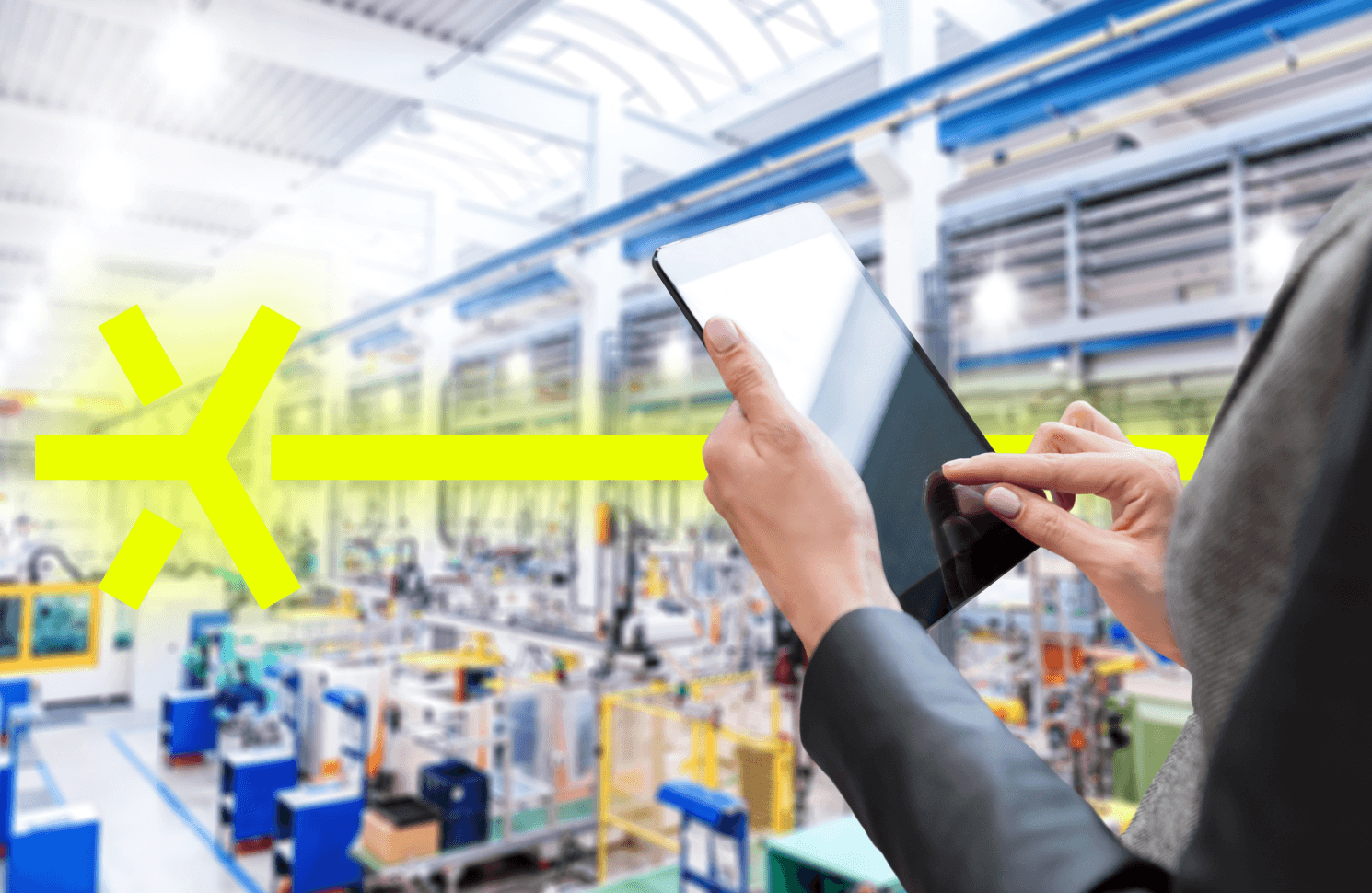
10 ways digital integrated manufacturing boosts efficiency for COOs in manufacturing
JUL. 18, 2025
3 Min Read
Your factory floor stands at a tipping point.
Data flows from machines, suppliers, and design teams, yet much of it sits in separate silos. Customers expect shorter lead times, regulators expect perfect traceability, and investors expect measurable gains. Closing these gaps calls for a production model built on connected data and synchronized processes.
Digital integrated manufacturing brings the people, systems, and assets of a plant into a single, coordinated network. Instead of chasing spreadsheets or waiting on delayed reports, operations leaders gain instant insight into status and performance. Teams can adjust schedules, quality thresholds, or maintenance windows based on live signals from the line. Such agility turns manufacturing from a cost center into a resilient profit generator.
key-takeaways
- 1. Digital integrated manufacturing aligns enterprise planning with real-time shop floor data for faster response to disruption.
- 2. Cloud-based platforms cut rollout timelines while providing centralized analytics and operational insights across multiple plants.
- 3. AI-powered forecasting improves resource planning, reducing stock-outs and overproduction by simulating optimal production runs.
- 4. Predictive maintenance and automated quality control reduce downtime, minimize rework, and protect margins without manual checks.
- 5. COOs gain greater agility, lower operating costs, and higher throughput through standardized digital workflows and integrated systems.
How digital integrated manufacturing impacts modern production models
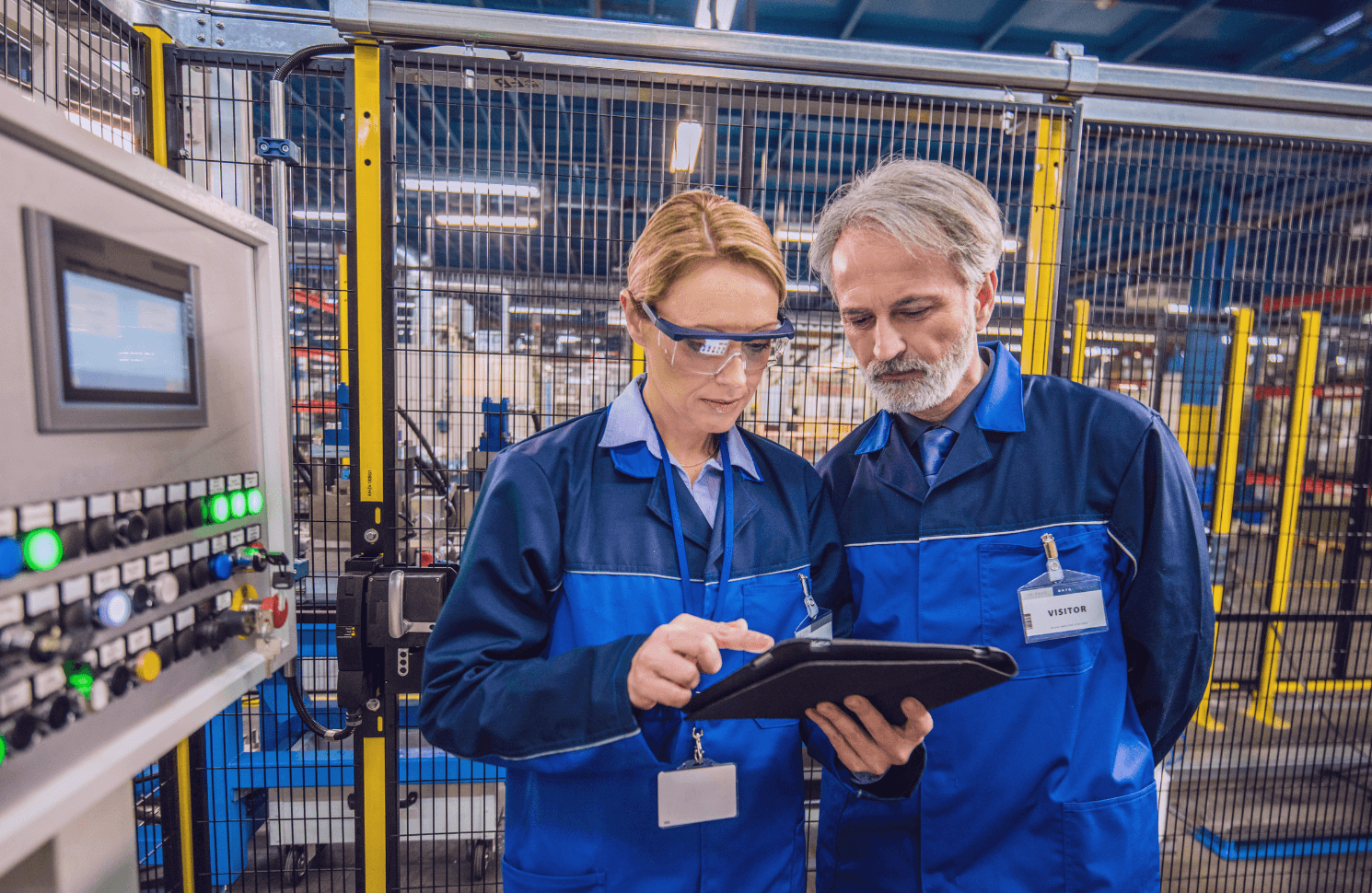
Manufacturing executives have long pushed for exact scheduling, yet legacy systems rarely talk to each other. Digital integrated manufacturing stitches enterprise resource planning, manufacturing execution, and industrial internet of things data into a unified model. This shared model delivers a single source of truth for orders, capacity, and quality metrics. As a result, planners adjust production in hours instead of days, and shop floor supervisors catch deviations before they trigger costly scrap.
The approach also reshapes how capital assets are utilized across multiple plants. Cloud connectivity lets remote experts diagnose performance issues, while AI services suggest parameter tweaks that raise throughput without new machines. Such shifts free cash for innovation and shorten the path from concept to commercialization. These advantages explain why modern manufacturing leaders view integration as an essential path to sustained growth.
“Digital integrated manufacturing brings the people, systems, and assets of a plant into a single, coordinated network.”
10 ways digital integrated manufacturing helps COOs lead modern manufacturing
Chief operating officers juggle delivery targets, quality mandates, and cost limits every quarter. Legacy processes force them to wait on yesterday’s reports before making production calls. A connected production framework slashes that delay by feeding live insights into strategic control towers. With clear data and synchronized workflows, operations leaders turn daily pressure into predictable performance.
1. Improved supply chain visibility with connected manufacturing systems
Supply shortages still threaten delivery promises, yet most plants only discover a material gap once it hits receiving. Connected systems link supplier portals, warehouse sensors, and production schedules, updating stock levels every few minutes. Planners see accurate inventory positions and inbound transit times without sending emails or making phone calls. That clarity prevents costly expedited fees and shrinks safety stock that ties up capital.
For example, a Midwest automotive Tier-1 supplier integrated purchase order data with machine sensors on its press lines. When a coil shipment faces a highway delay, the system automatically re-sequences jobs that use on-site materials first. The line keeps running, and the supplier meets its customer’s pickup window. This proactive stance builds trust across the chain and advances pay-for-performance contracts.
2. Real-time data sharing across enterprise and shop floor operations
Different levels of the organization often speak separate data dialects. Finance watches standard cost variance, while operators focus on cycle time and scrap. Digital integrated manufacturing translates machine tags into business metrics so both teams react to the same facts at the same moment. Fast alignment speeds up approvals for overtime, maintenance shifts, or rush orders.
A plastics producer linked its MES to a self‑service analytics portal used by regional general managers. The portal refreshes every 30 seconds, showing actual margin per part instead of aggregate plant averages. Managers decide whether to divert capacity to higher‑margin items before the mold cools. That minute‑level control can lift contribution by 3% in the first quarter after deployment.
3. Reduced downtime using predictive maintenance capabilities
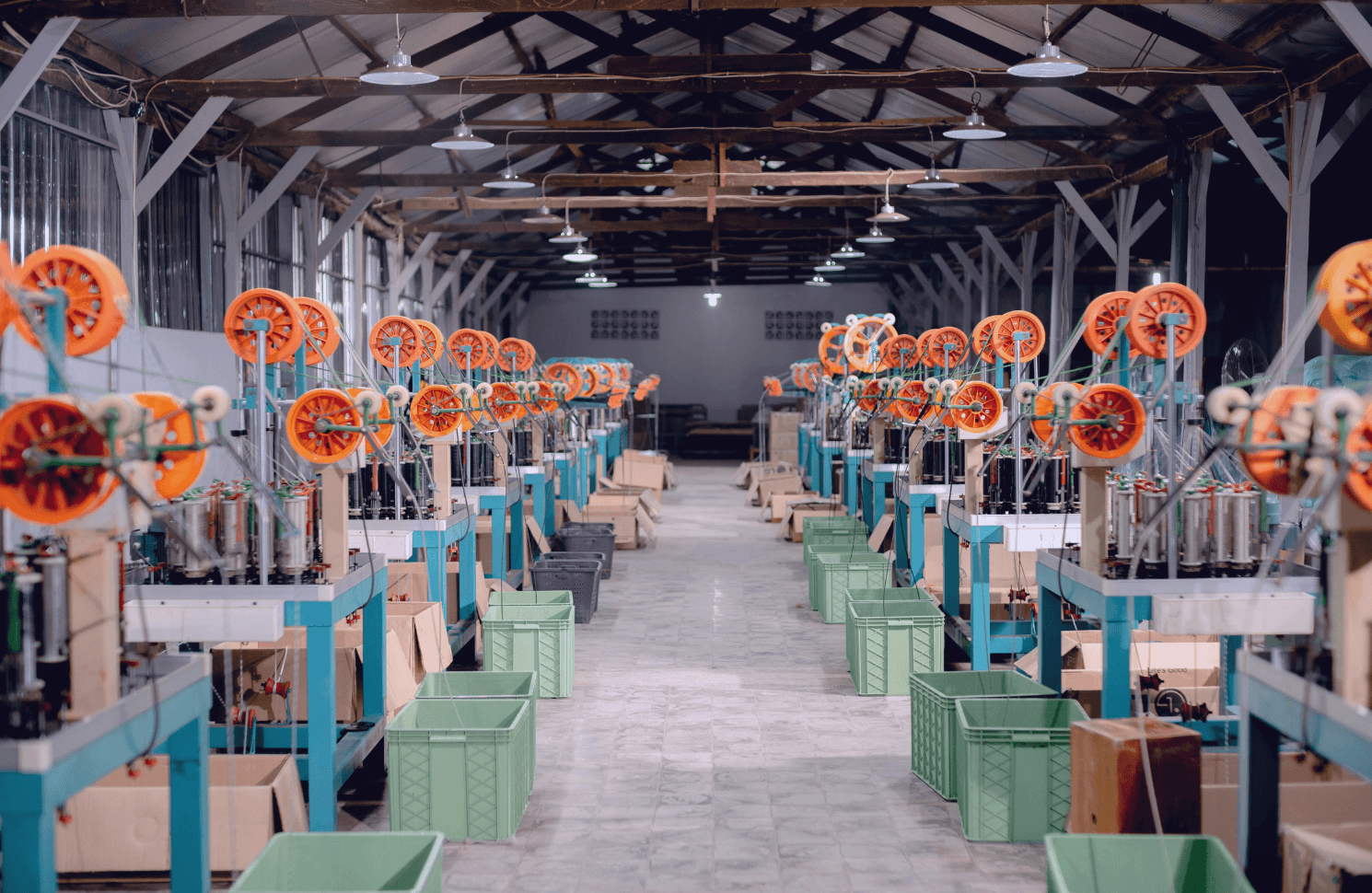
Unexpected breakdowns drain profit faster than almost any other issue. Sensor streams combined with histories of temperature, vibration, and power draw let algorithms spot early wear patterns. Maintenance planners schedule repairs during planned micro‑stops or shift changeovers instead of after a failure. Less stoppage keeps on‑time delivery metrics high and overtime low.
An electronics contract manufacturer analyzed pick‑and‑place head movement and discovered subtle drag increases before placement errors surfaced. After a parameter adjustment and a quick bearing swap, uptime rose to 98%, and scrap dropped 12%. The investment paid back within a single month due to saved rework labor. That result shows how predictive techniques pay off at both the line and enterprise scale.
4. Automated quality control with integrated IoT and analytics
Manual inspections often catch defects late, forcing rework or credits. High‑resolution cameras and torque sensors feed data to edge analytics that apply tolerance rules in milliseconds. The system flags out‑of‑spec parts instantly and instructs robots to divert them to a review station. Human inspectors focus on root cause investigation instead of repetitive checks.
A beverage plant applied this approach to cap torque readings on every bottle. When torque drifted, the capper tightened within three cycles, preventing leaks without a full line stop. Customer complaints dropped to nearly zero, and production volume grew because the plant avoided prolonged sanitation cycles. Automated assurance raises both product quality and brand reputation.
5. Faster time to market through digital process synchronization
Launching a new product often means days of debugging between design and production documents. Version‑controlled process plans automatically feed machine programs, tooling lists, and operator instructions from a single change request. When engineering updates tolerances, the adjusted parameters reach the line within minutes instead of overnight. This immediacy slashes pilot build cycles and wins market share with early product availability.
A household appliance maker credited synchronized planning for a 25‑day reduction in launch timeline for its latest induction cooktop. Digital verification caught clearance conflicts between the heating coil and housing before tooling build, saving $300 000. The same data packet later drove automated setup on the assembly cell, avoiding manual reprogramming. Shorter launch windows also reduce revenue risk from competitor releases.
6. Enhanced production planning using AI‑driven forecasting tools
Traditional planning relies on weekly spreadsheets that smooth order volume and hide variability. Machine‑learning models consume current POS data, economic indicators, and plant capacity figures to recommend schedule changes every hour. Planners simulate alternate runs and pick the mix that maximizes profit contribution. The result is fewer changeovers and steadier asset utilization.
A cosmetics firm layered neural nets on its historical sales data and seasonal promotions. The tool signaled a lipstick color surge six weeks ahead of a peak, giving suppliers enough notice to provide pigment with standard freight. Production ramped seamlessly, and the retailer avoided stock‑outs. Accurate forecasting cuts rush fees and keeps shoppers loyal.
7. Seamless coordination between design engineering and manufacturing
Design changes often reach production through static PDFs that require manual interpretation. A shared product data hub pushes updates directly into CAD viewers and MES screens, removing phone calls and email threads. Operators always see the latest revision, and engineers watch run data to confirm performance against design intent. This closed loop narrows the gap between concept and output.
During a medical device recall, one life‑sciences producer used this loop to adjust welding parameters within two days of a regulatory notice. Traceable links between drawing versions and batch numbers provided instant evidence for auditors. The company contained risk without halting global shipments. Coordination at that speed protects both revenue and public safety.
8. Increased efficiency from cloud‑based manufacturing platforms
On‑premises servers limit scalability and strain small IT teams during upgrades. Cloud‑based MES and SCADA services update automatically and allocate processing power during usage peaks, lowering hardware spend. Plants roll out new analytics modules with a configuration file instead of weeks of provisioning. Shared dashboards show performance across sites, letting leaders compare best practices and standardize quickly.
A consumer‑electronics OEM moved OEE (overall equipment effectiveness) analytics to a secure multi‑tenant cloud. Deployment time for each facility dropped from four months to four weeks, saving nearly $2 million in integration fees. Central storage also simplified data retention rules for compliance. Efficiency gains compensate for subscription costs within the first fiscal year.
9. Cost reductions through leaner, digitally coordinated workflows
Paper travelers, manual sign‑offs, and hand‑written log books slow every job. Digital workflows route approvals, collect signatures, and update status bars in the same system that drives machines. Queues shrink, and process engineering teams redirect hours toward improvement projects. Reduced waste translates directly into margin growth.
One specialty chemical producer eliminated 2,700 paper sheets daily by shifting from batch cards to e‑sign tablets. The change saved $250,000 annually in printing and archiving costs while also improving operator accountability. Audit time fell because reports were already sorted by lot number and data tag. Savings stack year after year once the paperwork disappears.
10. Standardized compliance reporting across distributed facilities
Regulatory agencies ask for precise batch histories, yet facilities often store them in varied formats. Digital integrated manufacturing aligns data schemas and timestamps across every site, producing consistent electronic batch records. Queries that once took a week run in minutes, cutting risk during inspections. A shared template also reduces consultant fees for local regulation reviews.
During a surprise US Food and Drug Administration audit, a biotech firm generated proof of sterilization cycles for three plants in under two hours. Cross‑site data integrity impressed inspectors and avoided a warning letter. Standardization protects licences and shortens the path to new product introductions. When compliance is routine, leaders focus on growth rather than paperwork.
Live data feeding coordinated action drives measurable progress across production. When systems speak the same language, COOs steer production with confidence rather than instinct. Digital integrated manufacturing delivers that clarity while strengthening resilience against supply shocks, equipment glitches, and workforce turnover. Adopting a connected approach turns reactive firefighting into deliberate performance tuning.
"Machine‑learning models consume current POS data, economic indicators, and plant capacity figures to recommend schedule changes every hour."
Want to learn how digital integrated manufacturing can bring more transparency and trust to your operations?
Why modern manufacturing examples are moving toward full integration
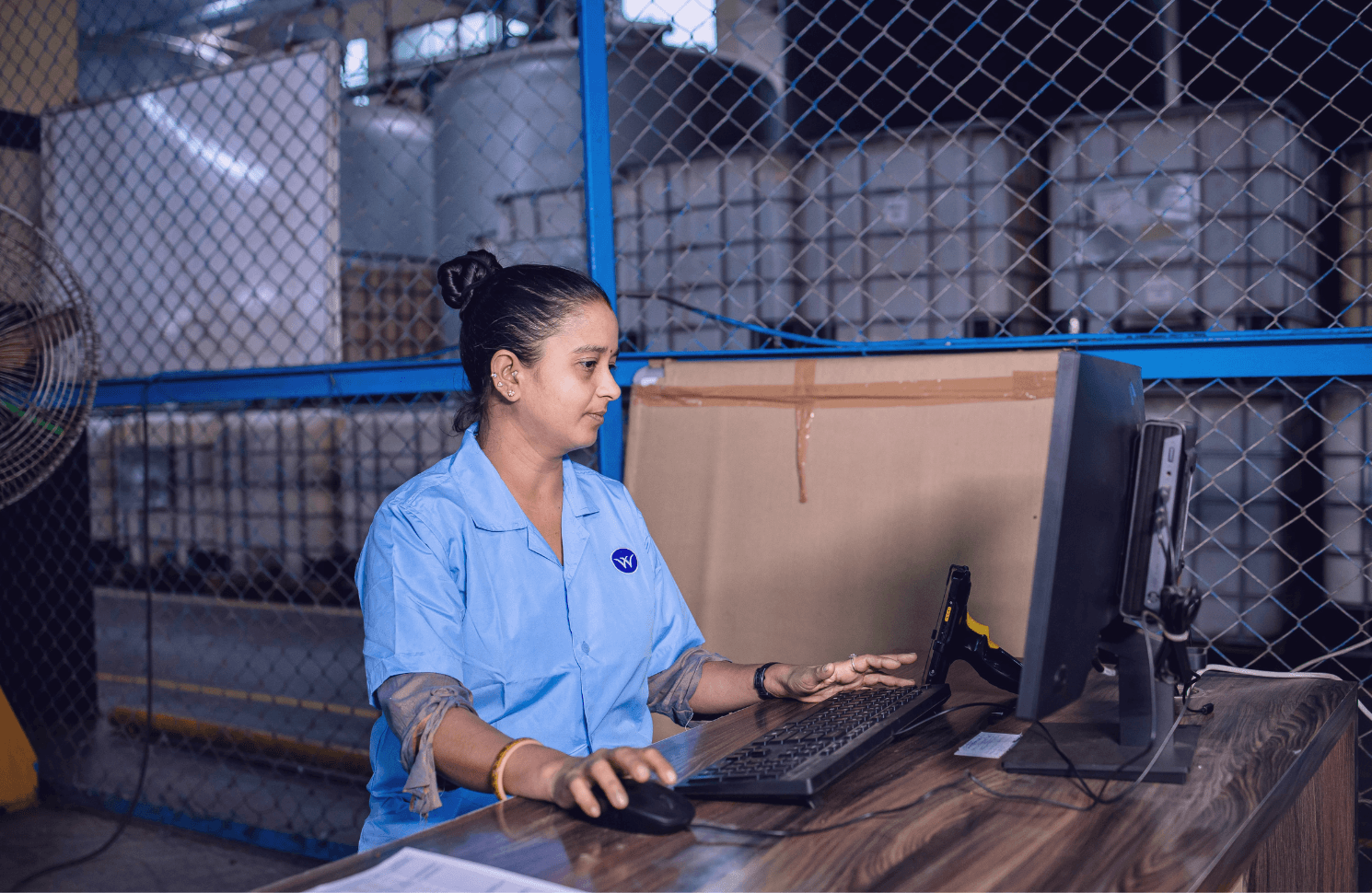
Investors judge manufacturing firms not only on cost but on their ability to adapt to market swings. Isolated applications make adaptation slow because each change ripples through spreadsheets and tribal knowledge before reaching the line. Full integration compresses that ripple into an automated update, so pricing shifts, new materials, or regulatory addenda flow directly to execution. Organizations that adopt this approach report shorter cash cycles and stronger predictability, which attracts additional capital.
Modern manufacturing examples from aerospace to food packaging reveal another incentive: workforce expectations. Digital natives expect intuitive dashboards, contextual help, and fewer manual inputs. Integrated systems supply those tools, raising retention and shortening training for replacement hires. Soft cost avoidance often matches hard savings, amplifying the impact of the integration strategy.
How Lumenalta helps COOs execute digital manufacturing at scale
Lumenalta partners with operations leaders to build a production ecosystem where data flows freely from sensor to boardroom. Our architects map existing hardware, software, and workflows, then prescribe an integration blueprint that aligns with your capital plan. Pre‑built connectors link common ERP, MES, and industrial IoT platforms, shaving months off launch timelines. We also coach plant engineers on configuration so improvements continue after the initial rollout. This hands‑on approach keeps ownership inside your team and guards against vendor lock‑in.
Scalability matters when you oversee multiple sites, so our cloud orchestration patterns replicate a validated design across every facility with role‑based access and regional compliance settings. A centralized metrics model surfaces real‑time OEE, energy usage, and quality trends, letting you allocate resources seconds after variance appears. Built‑in AI services recommend maintenance windows and production mixes that protect margin without risking service level penalties. Reference cases show payback periods under twelve months and sustained EBIT growth over three years. Choose a partner that blends technical rigor with strategic insight, and trust that Lumenalta will deliver measurable results.
table-of-contents
- How digital integrated manufacturing impacts modern production models
- 10 ways digital integrated manufacturing helps COOs lead modern manufacturing
- 1. Improved supply chain visibility with connected manufacturing systems
- 2. Real-time data sharing across enterprise and shop floor operations
- 3. Reduced downtime using predictive maintenance capabilities
- 4. Automated quality control with integrated IoT and analytics
- 5. Faster time to market through digital process synchronization
- 6. Enhanced production planning using AI‑driven forecasting tools
- 7. Seamless coordination between design engineering and manufacturing
- 8. Increased efficiency from cloud‑based manufacturing platforms
- 9. Cost reductions through leaner, digitally coordinated workflows
- 10. Standardized compliance reporting across distributed facilities
- Why modern manufacturing examples are moving toward full integration
- How Lumenalta helps COOs execute digital manufacturing at scale
- Common questions about digital integrated manufacturing
Common questions about digital integrated manufacturing
How can I improve supply chain resilience in manufacturing?
What is the value of AI in modern manufacturing operations?
Why should I integrate IoT devices into my production line?
How does digital manufacturing reduce operational costs?
What’s the difference between traditional MES and cloud-based manufacturing platforms?
Want to learn how digital integrated manufacturing can bring more transparency and trust to your operations?