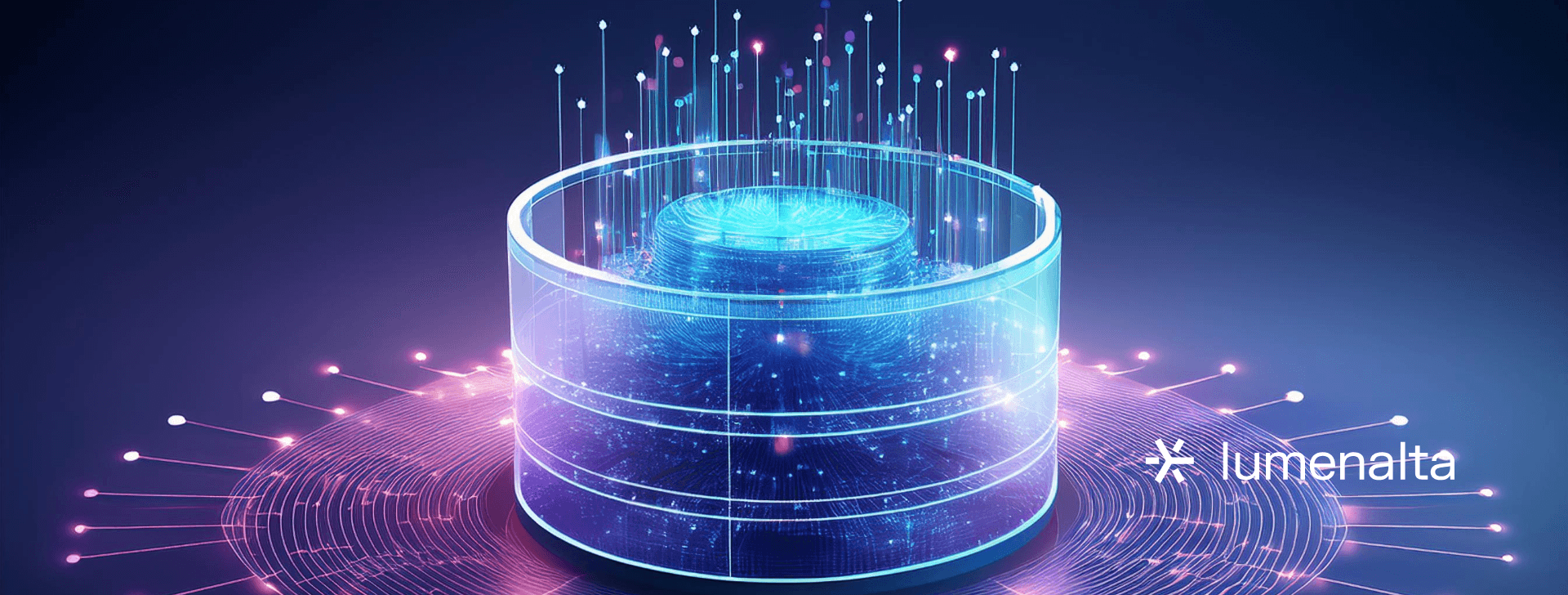
What is product data management? PDM vs PLM vs PIM
APR. 25, 2024
7 Min Read
Managing product data efficiently is essential for keeping production timelines on track, reducing costly errors, and maintaining collaboration between engineering, manufacturing, and procurement teams.
Disorganized product information leads to misplaced files, incorrect specifications, and unnecessary rework that impacts profitability. Product data management (PDM) centralizes technical data, eliminates inconsistencies, and creates structured workflows that improve efficiency. As organizations scale operations and adopt more complex product development processes, selecting the right PDM system ensures data integrity, improves accuracy, and strengthens operational workflows.
Key takeaways
- 1. PDM eliminates inconsistencies and improves collaboration by centralizing product data, reducing errors, and streamlining communication between engineering, procurement, and manufacturing teams.
- 2. Automation strengthens PDM workflows with AI-powered insights, automated version control, and structured approval processes that reduce manual workload and improve efficiency.
- 3. Cloud-based and hybrid PDM solutions provide scalable, flexible options that reduce infrastructure costs and improve remote accessibility for teams working across multiple locations.
- 4. Seamless integration with ERP, PLM, and MES systems eliminates data silos, improves accuracy, and ensures teams work with the latest product specifications.
- 5. PDM plays a critical role in regulatory compliance by maintaining structured records, automating audit trails, and tracking design revisions to meet industry standards.
What is product data management?
Organizing and maintaining product-related data is essential for businesses looking to improve operational efficiency, reduce errors, and accelerate production cycles. Product data management (PDM) provides a structured approach to storing, accessing, and controlling vital information across product development, engineering, manufacturing, and procurement teams. Departments rely on disconnected files and manual updates without a centralized system, leading to inconsistencies, wasted resources, and costly delays. PDM eliminates these risks by consolidating design files, technical specifications, and revision histories into a single, accessible repository.
A well-structured PDM system improves collaboration and version control by automating data tracking and reducing reliance on outdated spreadsheets or disjointed databases. Engineers and product managers can work confidently with accurate information, while procurement teams benefit from real-time access to up-to-date materials lists and supplier details. PDM also integrates with enterprise resource planning (ERP) and product lifecycle management (PLM) systems to support seamless data flow between departments.
Selecting the right PDM approach impacts more than internal efficiency. Faster time to market, better compliance with industry regulations, and stronger coordination across teams contribute to measurable business gains. A scalable PDM strategy allows companies to adapt to market shifts without risking product quality or regulatory misalignment.
Key product data management capabilities
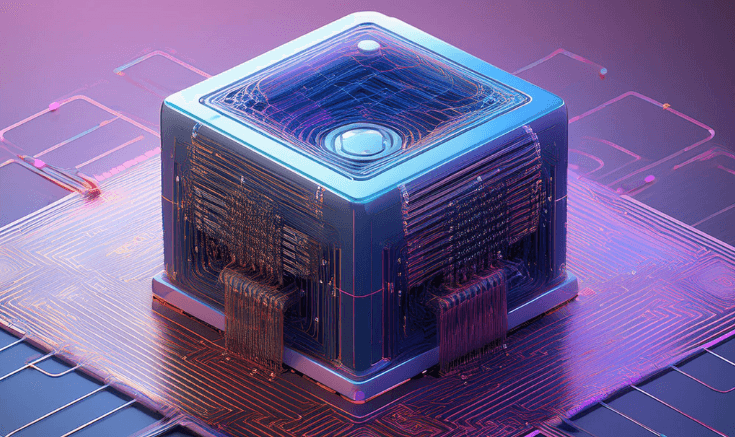
Centralized data storage and structured organization
A PDM system consolidates all product-related information into a single, structured repository. Technical drawings, CAD files, bills of materials (BOMs), and compliance documents remain organized and easily retrievable, reducing time wasted on manual searches. Metadata tagging, search filters, and classification structures improve accessibility, allowing teams to locate the correct data without delays.
Version control and structured revision tracking
Managing product iterations requires clear documentation of every change. PDM solutions track revisions automatically, providing a complete history of modifications and approvals. Engineers and designers can access previous versions when needed, minimizing errors that occur from using outdated information. Structured approval processes keep changes aligned with compliance requirements, reducing risks associated with unauthorized modifications.
Secure access control and role-based permissions
Sensitive product data requires controlled access to prevent unauthorized changes or exposure. PDM systems assign user roles and permissions based on job functions, limiting modifications to designated individuals. Engineers may have full editing access, while procurement and production teams may only view finalized specifications. Structured access control reduces the risk of accidental alterations and strengthens data security protocols.
Streamlined collaboration and automated workflows
A structured PDM system enhances coordination across departments by integrating CAD software, enterprise resource planning (ERP) platforms, and manufacturing execution systems (MES). Automated notifications alert teams to pending approvals, changes, or required updates, eliminating communication gaps. Workflow automation reduces reliance on manual tracking, helping teams meet production timelines more efficiently.
Compliance management and audit-ready documentation
Industry regulations require accurate product documentation to validate safety, performance, and quality standards. A structured PDM system centralizes all compliance-related files, making audit processes more efficient. Change histories, approvals, and certifications remain accessible for internal or external reviews. Consistently maintaining accurate records reduces regulatory risks and improves accountability across teams.
A PDM system is more than a data repository—it provides structured workflows, improves collaboration, and protects product integrity. With a well-implemented system, businesses can minimize production errors, accelerate approvals, and improve operational efficiency while keeping product data aligned with compliance and quality standards.
"Managing product-related data efficiently reduces errors, accelerates production cycles, and improves collaboration across teams."
PDM vs. PLM vs. PIM
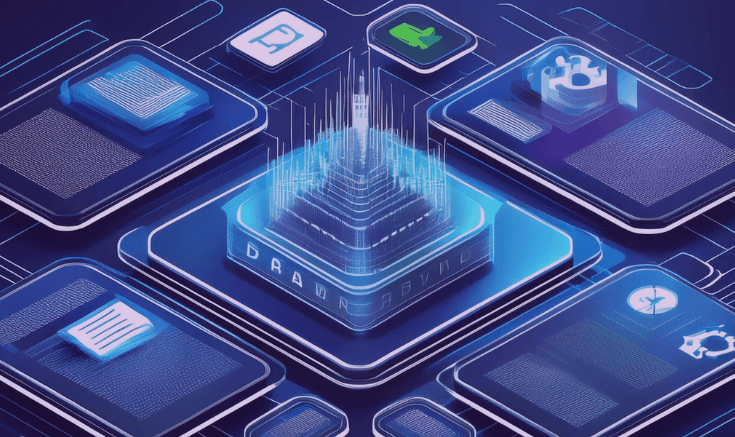
PDM focuses on technical data within engineering and manufacturing processes, ensuring design files, bills of materials (BOMs), and version histories remain accurate and accessible. PLM extends beyond PDM, managing the entire product lifecycle from initial concept to disposal. Conversely, PIM centralizes product information used in marketing, sales, and e-commerce, allowing businesses to maintain consistency across multiple sales channels. Each system integrates with different enterprise solutions, serving unique but complementary roles.
Feature | PDM (Product Data Management) | PLM (Product Lifecycle Management) | PIM (Product Information Management) |
---|---|---|---|
Primary Function | Organizes and controls technical product data | Manages product lifecycle from concept to retirement | Centralizes product marketing and sales-related information |
Users | Engineers, designers, manufacturing teams | Cross-functional teams including engineering, procurement, and operations | Marketing, sales, and e-commerce teams |
Data Managed | CAD files, engineering drawings, BOMs, and revision histories | Product development workflows, compliance records, and approvals | Product descriptions, images, pricing, and digital assets |
Integration Focus | CAD software, ERP, and MES | ERP, supply chain systems, CRM, and quality management tools | E-commerce platforms, digital catalogs, and ERP systems |
Scope | Controls product documentation and version tracking | Oversees development, compliance, and cross-team collaboration | Supports omnichannel distribution and content consistency |
Outcome | Streamlined data management for engineering teams | End-to-end coordination across the product lifecycl | Accurate, centralized product information for sales and marketing |
PDM, PLM, and PIM each contribute to operational efficiency in distinct ways. Engineering teams rely on PDM to manage design data and prevent inconsistencies, while PLM connects product development with supply chain and quality management processes. PIM ensures accurate product information across multiple sales channels, improving marketing performance and customer experience. Selecting the right solution depends on business priorities, the complexity of product data, and the level of integration required across departments.
Benefits of product data management
Organizing product-related data effectively reduces errors, minimizes production delays, and improves team coordination. Without a structured approach, misplaced files, outdated specifications, and version conflicts slow development and create costly inefficiencies. Product data management (PDM) centralizes technical information, keeping records accurate and accessible while integrating with other enterprise systems to streamline workflows. Engineering, procurement, and manufacturing teams benefit from a system that reduces miscommunication, prevents unnecessary rework, and supports better planning.
PDM solutions provide measurable advantages across multiple departments, improving accuracy, accelerating product development, and supporting compliance requirements. The impact of a well-structured system extends beyond data organization, affecting overall operational efficiency and business outcomes.
- More accurate version control: Design teams work with the latest product specifications, avoiding costly mistakes caused by outdated files. Automatic tracking logs modifications, making reviewing previous versions easier and maintaining consistency.
- Shorter production cycles: Delays caused by missing or incorrect data slow development and manufacturing processes. A structured PDM system provides instant access to required files, reducing time spent searching for information and expediting approvals.
- Stronger coordination across departments: Engineers, manufacturing teams, and procurement specialists work from the same centralized repository, eliminating misalignment caused by disconnected files and manual updates. Structured workflows keep processes efficient and prevent unnecessary back-and-forth communication.
- Simplified regulatory compliance: Industry standards require detailed records of product designs, material specifications, and testing data. A well-organized PDM system keeps all documentation in one place, making audits easier and reducing compliance risks.
- Lower costs through reduced rework: Incorrect data often leads to production errors, wasted materials, and additional labor. A structured approach to product data management reduces these risks by keeping specifications accurate and easily accessible.
- Stronger integration with enterprise systems: PDM connects with enterprise resource planning (ERP), product lifecycle management (PLM), and manufacturing execution systems (MES), allowing teams to work with synchronized data across all stages of development and production.
A well-structured PDM strategy eliminates inefficiencies caused by disorganized data, helping teams complete projects faster while minimizing risks. Centralizing product information improves overall productivity, making it easier to maintain accuracy, reduce delays, and maximize long-term business value.
Types of product data management solutions
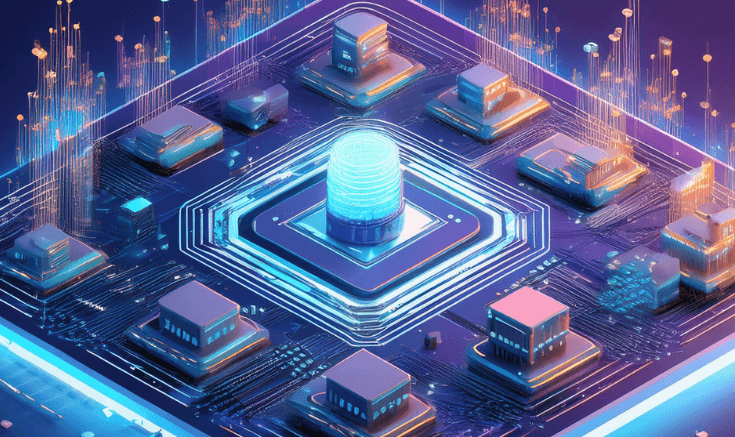
PDM solutions fall into several categories, each designed to meet specific operational needs. Some organizations prioritize complete control over data storage, while others require remote accessibility and scalability. Hybrid models offer flexibility, and industry-specific systems provide tailored compliance features for regulated sectors.
On-premise PDM solutions
On-premise PDM systems store data within an organization’s internal infrastructure, offering full security oversight, customization, and compliance oversight. Engineers and manufacturers working with proprietary product designs or confidential technical documents often require this level of control. IT teams manage updates, system performance, and user permissions to maintain operational reliability. While on-premise systems provide strong security, they often require significant hardware investment, ongoing maintenance, and dedicated IT support.
Cloud-based PDM solutions
Cloud-based PDM solutions store product data on secure external servers, allowing teams to access files remotely through web-based platforms. These systems improve collaboration by providing real-time access to product specifications, design files, and revision histories. Automatic software updates, built-in scalability, and lower upfront costs make cloud-based solutions practical for organizations prioritizing flexibility. Engineering and procurement teams benefit from streamlined workflows, eliminating the inefficiencies caused by versioning conflicts or misplaced files.
Hybrid PDM solutions
Hybrid PDM systems combine elements of both on-premise and cloud-based platforms. This approach allows organizations to store critical data on internal servers while using cloud-based tools for collaboration and remote accessibility. Companies working with sensitive information often require this level of control while still benefiting from cloud-based scalability. A hybrid model provides flexibility in managing security requirements while improving accessibility for distributed teams.
Industry-specific PDM solutions
Certain industries require PDM solutions designed to align with strict regulatory and compliance requirements. Aerospace, automotive, and medical device manufacturers depend on industry-specific platforms that include built-in compliance tracking, automated reporting, and specialized workflows. These systems integrate with existing enterprise resource planning (ERP) and manufacturing execution system (MES) platforms to maintain consistency across development and production processes.
A structured approach to selecting a PDM solution improves data accuracy, strengthens collaboration, and minimizes inefficiencies. Each type of system offers unique advantages based on security requirements, operational complexity, and long-term scalability. Implementing the right PDM solution optimizes workflows, improves product data integrity, and supports seamless coordination across departments.
How to choose the right PDM software
Selecting a product data management (PDM) system affects how efficiently teams collaborate, manage product information, and maintain compliance with industry regulations. Without a structured system, version control issues, miscommunication, and data inconsistencies slow production and increase operational costs. Engineering, procurement, and manufacturing teams rely on accurate product data to streamline processes and minimize errors. The right PDM software improves efficiency, reduces rework, and provides a structured approach to managing product information across departments.
A PDM system must integrate with existing enterprise resource planning (ERP), product lifecycle management (PLM), and manufacturing execution system (MES) platforms to maintain data consistency. Teams struggle with disconnected files and outdated specifications without seamless integration, leading to production errors and wasted resources. Scalability also plays a key role in selecting a PDM system. Organizations expanding product lines or entering new markets need a system that adapts to increased data volumes and operational complexity. Cloud-based and hybrid solutions offer flexible storage and accessibility, allowing teams to scale without technical limitations.
Security and access control remain critical, especially in industries managing proprietary designs and regulated data. A PDM system with role-based permissions prevents unauthorized modifications, allowing designated personnel to retrieve necessary files. Protecting intellectual property and sensitive product details requires encryption, audit trails, and controlled access based on job roles. Usability also affects how quickly teams adopt a PDM system. A complicated interface slows productivity, while an intuitive platform reduces training time and increases adoption across departments. Systems with structured search functions, automated workflows, and version tracking improve efficiency without requiring extensive onboarding.
Regulatory compliance adds another layer of complexity to PDM selection. Industries subject to strict documentation requirements need a system that maintains accurate records, tracks revisions, and provides audit-ready data. Automating compliance tracking reduces manual errors and simplifies reporting processes. A PDM system with structured workflows, built-in approval processes, and automated change tracking reduces compliance risks while improving operational efficiency.
A structured approach to selecting a PDM system eliminates inefficiencies, minimizes risks, and supports long-term growth. Software that integrates with existing systems, scales with operational needs, protects data integrity, simplifies compliance, and improves efficiency across engineering, procurement, and manufacturing teams. Investing in the right PDM solution streamlines collaboration, reduces production delays, and maximizes business value.
Best practices for implementing product data management
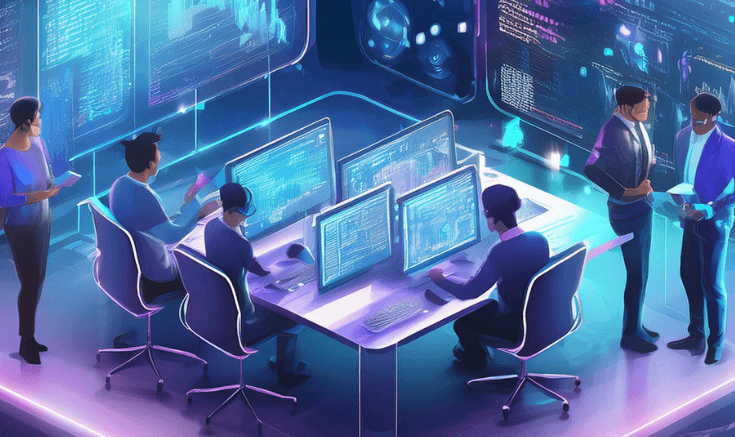
Define clear objectives and requirements
Understanding business needs before implementing a PDM system ensures that the selected solution aligns with operational goals. Engineering, procurement, and manufacturing teams must identify data storage, version control, and collaboration challenges. Establishing clear objectives helps organizations select a system that integrates with existing enterprise resource planning (ERP) and product lifecycle management (PLM) platforms, ensuring seamless data synchronization across departments.
Standardize data structures and naming conventions
Inconsistent file names, duplicate records, and unstructured metadata make retrieving and managing product information difficult. Establishing uniform naming conventions and categorization rules improves accessibility and reduces confusion. Standardized data structures allow engineering and procurement teams to locate files quickly while maintaining consistency across product lines and revisions.
Establish access controls and user permissions
Managing product data securely requires defining user roles and permissions to prevent unauthorized modifications. Engineers, designers, and production teams need different levels of access based on job functions. A structured approach to permissions ensures that sensitive product data remains protected while allowing authorized personnel to retrieve necessary files. Audit trails and activity logs provide additional security, tracking modifications and approvals to maintain data integrity.
Train teams for system adoption
A PDM system delivers the most value when teams understand how to use it effectively. Providing structured training sessions and documentation accelerates adoption while reducing productivity losses during the transition. Engineering and procurement teams benefit from role-based training focusing on search functions, version control, and workflow automation. Ongoing support ensures users can troubleshoot issues and maximize the system’s capabilities.
Automate workflows and approval processes
Manual data entry, approval tracking, and revision control slow production and increase errors. A well-implemented PDM system automates these processes, reducing delays and improving efficiency. Structured approval workflows notify the proper personnel when changes require review, eliminating bottlenecks and minimizing miscommunication. Automating data synchronization with ERP and PLM systems improves data accuracy across departments.
A structured approach to PDM implementation allows organizations to maximize efficiency, reduce errors, and maintain accurate product records. Standardized data structures, secure access controls, automated workflows, and proper training help teams optimize system usage while minimizing disruptions. A well-executed strategy improves department collaboration, supports compliance requirements, and accelerates product development cycles.
The role of automation in PDM
Managing product data manually increases the risk of errors, slows production workflows, and creates bottlenecks that affect operational efficiency. Engineering, procurement, and manufacturing teams rely on accurate, up-to-date product information to coordinate efforts and minimize rework. Automating product data management (PDM) eliminates inconsistencies, reduces approval delays, and improves overall productivity by synchronizing data across teams and integrating with enterprise systems. Structured automation replaces manual tracking with efficient workflows that help organizations manage product lifecycles more effectively.
Version control automation prevents issues caused by outdated product files. Engineering teams frequently update product specifications, making it essential to maintain a structured record of modifications. Manual tracking often results in version conflicts, production errors, costly material waste, and compliance risks. A PDM system records and organizes every modification, keeping all teams aligned with the most current specifications. Revision histories remain accessible for quality control, regulatory audits, and supplier coordination, reducing unnecessary back-and-forth communication.
Workflow automation improves efficiency by streamlining approvals, change requests, and data validation processes. Engineers and procurement teams receive real-time notifications when modifications impact sourcing, allowing adjustments before production begins. Delays caused by miscommunication decrease when structured approval workflows route tasks to the right personnel. Notifications for pending actions keep projects moving, while automated compliance tracking simplifies documentation and reporting for industry regulations. These structured workflows allow organizations to reduce approval times and maintain quality standards without unnecessary manual oversight.
Integrating enterprise resource planning (ERP) and product lifecycle management (PLM) systems eliminates redundant data entry and inconsistencies across departments. A structured PDM system synchronizes product data across development, manufacturing, and supply chain operations, reducing the likelihood of errors caused by outdated or disconnected information. Procurement teams access accurate bills of materials (BOMs), manufacturing teams work with updated specifications, and quality assurance teams validate compliance without the inefficiencies of manual updates.
Automating PDM processes strengthens collaboration, eliminates data inconsistencies, and improves production efficiency across departments. Version control, workflow automation, compliance tracking, and enterprise system integration reduce errors and create a structured approach to managing product information. A well-implemented automation strategy allows organizations to maintain accurate records, minimize production delays, and improve operational efficiency.
Addressing key challenges in PDM
Managing product data effectively requires a structured approach that eliminates inefficiencies, reduces miscommunication, and supports team collaboration. Without a centralized system, engineering, manufacturing, and procurement teams encounter challenges that slow production cycles, increase costs, and introduce errors into product development workflows. A well-implemented product data management (PDM) system resolves many of these issues, but several common challenges must be addressed to maximize its effectiveness.
- Inconsistent data across departments: Engineering, procurement, and manufacturing teams often rely on separate systems to manage product information, leading to data discrepancies and miscommunication. A centralized PDM system eliminates inconsistencies by maintaining a single source of accurate product information.
- Version control issues: Manual tracking of design revisions and specifications results in outdated or conflicting data, increasing the risk of production errors. Automated version control records every modification, preventing teams from working with incorrect files and reducing costly rework.
- Limited integration with enterprise systems: Disconnected PDM systems create inefficiencies by requiring manual data entry across enterprise resource planning (ERP), product lifecycle management (PLM), and manufacturing execution systems (MES). Seamless integration allows product data to remain consistent across all operational workflows.
- Access control and data security concerns: Unauthorized modifications or accidental deletions compromise product integrity and create compliance risks. Role-based access controls ensure only authorized personnel can modify or approve changes while maintaining secure access for other users.
- Regulatory compliance and audit readiness: Industries subject to strict documentation and quality standards require structured compliance tracking. A well-implemented PDM system automates record-keeping, maintains audit trails, and provides a structured repository for regulatory documentation.
- User adoption and training challenges: Teams unfamiliar with structured data management may struggle to transition to a new system. Proper training, user-friendly interfaces, and role-based access simplify adoption and improve productivity without disrupting workflows.
Structured PDM implementation improves efficiency, reduces risks, and strengthens department collaboration. Addressing data inconsistencies, automating version control, integrating with enterprise systems, and enhancing access security create a more reliable approach to managing product information. Organizations that prioritize these solutions reduce errors, accelerate production cycles, and maintain compliance with industry regulations.
"A well-implemented product data management (PDM) system resolves many of these issues, but several common challenges must be addressed to maximize its effectiveness."
Future trends in product data management
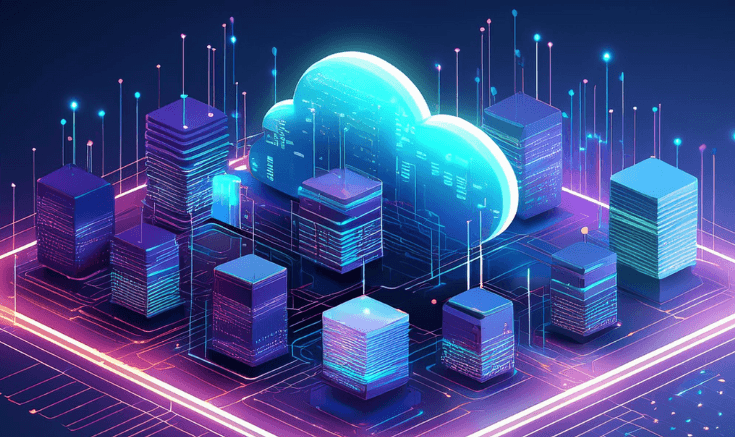
AI and machine learning (ML) improve data accuracy by automating classification, detecting inconsistencies, and predicting potential errors before they affect production. Engineering and procurement teams benefit from AI-powered search functions that retrieve design files, specifications, and revision histories without manual filtering. Automated recommendations also improve workflow efficiency by suggesting relevant components, materials, and compliance documentation based on historical data. These capabilities minimize administrative tasks, allowing teams to focus on higher-value engineering and manufacturing processes.
Cloud-based PDM solutions continue to expand, offering greater accessibility, flexibility, and lower infrastructure costs. Traditional on-premise systems require dedicated IT management and significant hardware investments, limiting scalability. Cloud-based platforms provide automatic updates, remote collaboration, and real-time data synchronization without extensive internal maintenance. Engineering and manufacturing teams working across multiple locations gain immediate access to the latest product data, reducing delays caused by outdated information. Hybrid solutions, combining on-premise security with cloud-based accessibility, provide an alternative for industries requiring strict data control while maintaining remote access.
Seamless integration between PDM, enterprise resource planning (ERP), product lifecycle management (PLM), and manufacturing execution systems (MES) is becoming standard practice. Structured data flows eliminate manual entry errors and align engineering, procurement, and production teams. Advances in API technology improve system connectivity, allowing product data to synchronize in real time across multiple platforms. More substantial integration capabilities support supply chain optimization by providing procurement teams instant access to material availability, supplier specifications, and compliance records.
Regulatory compliance remains a priority, with automated compliance tracking improving organizations' management of audits and industry standards. PDM systems now include built-in workflows that track approvals, generate audit-ready reports, and maintain a complete record of certifications and regulatory filings. These capabilities help engineering and quality assurance teams avoid compliance risks while reducing administrative work.
Advancements in automation, cloud accessibility, AI-powered insights, and system integration are shaping the future of PDM. These improvements reduce inefficiencies, strengthen data accuracy, and improve department collaboration. Organizations adopting modern PDM solutions position themselves for long-term scalability, operational efficiency, and structured product data management that aligns with industry requirements.
Product data management is more than a technical necessity—it is a strategic foundation for operational efficiency, accuracy, and business growth. Structuring product information eliminates inefficiencies, reduces production delays, and strengthens department collaboration. At Lumenalta, we specialize in building PDM solutions tailored to your business goals, ensuring your teams work with accurate, scalable, and secure data. Let’s create a brighter path to efficiency together.
table-of-contents
- What is product data management?
- Key product data management capabilities
- PDM vs. PLM vs. PIM
- Benefits of product data management
- Types of product data management solutions
- How to choose the right PDM software
- Best practices for implementing product data management
- The role of automation in PDM
- Addressing key challenges in PDM
- Future trends in product data management
- Common questions about product data management
Common questions about product data management
What is product data management, and why is it important?
What is the difference between PDM, PLM, and PIM?
How does automation improve PDM?
What industries benefit most from PDM?
How can PDM improve regulatory compliance?
Want to learn how product data management can bring more transparency and trust to your operations?