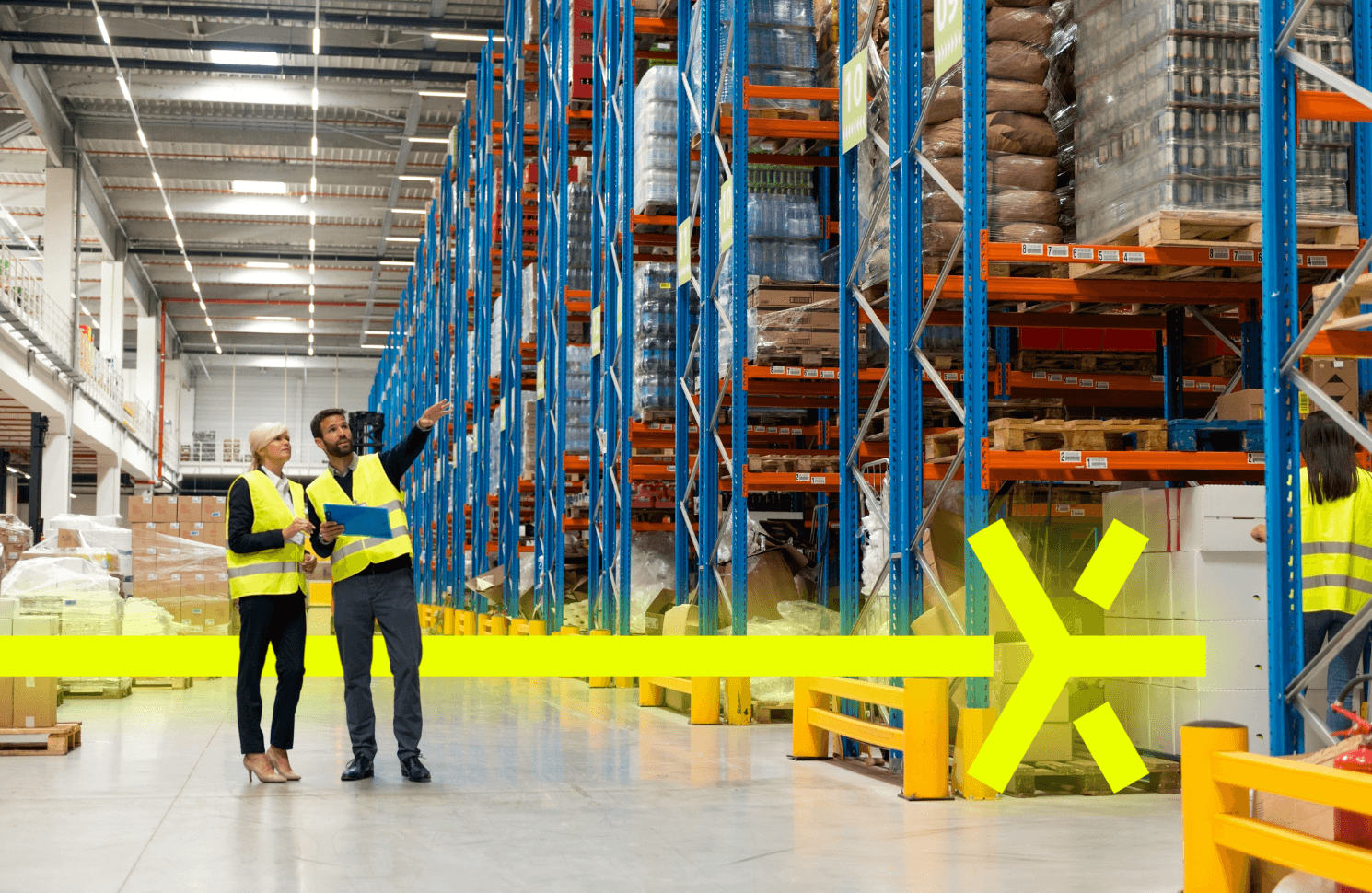
7 practical ways COOs use AI to streamline warehouse management
JUL. 4, 2025
9 Min Read
Every operations leader wants to sleep at night knowing tomorrow’s orders will leave the dock on schedule.
Missed shipments ripple through margins, customer satisfaction scores, and brand reputation. Artificial intelligence now offers a route to accuracy that manual spreadsheets cannot match. Shifting from guesswork to data‑guided action lifts both cost control and delivery speed.
Warehouses produce a torrent of data from scanners, sensors, and routing systems. When that data sits unused, trucks idle, and pickers search for items that should be front and center. Machine learning models learn from historical patterns and provide precise guidance on what to stock, where to stock it, and how staff should move. As capital budgets tighten, leaders want every square foot and every labor hour to return measurable value.
key-takeaways
- 1. AI tools like forecasting, routing, and quality inspection are giving COOs better control over warehouse cost and accuracy.
- 2. Autonomous robots and real-time labor allocation software are cutting down on travel time, congestion, and human error.
- 3. Predictive maintenance and inventory insights reduce unplanned downtime and working capital requirements.
- 4. Strategic AI integration creates scalable systems that respond faster to volume swings and service level expectations.
- 5. Operations leaders are prioritizing warehouse AI to align with executive goals around ROI, reliability, and cost efficiency.
Why AI in warehouse management is a priority for COOs
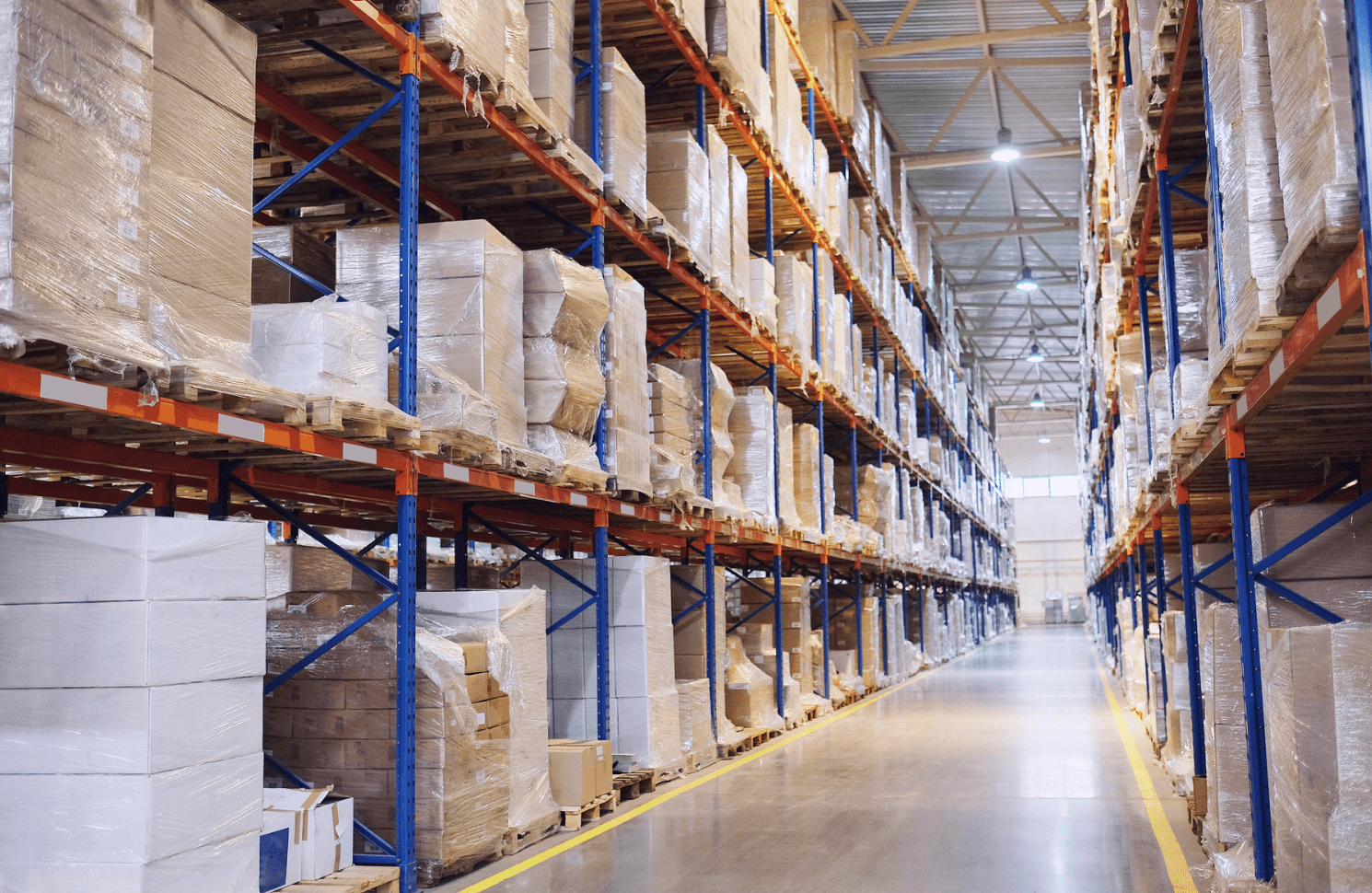
COOs feel daily pressure to shorten pick‑to‑ship cycle time without sacrificing accuracy. Traditional warehouse execution systems rely on static rules that struggle during promotions, seasonal peaks, or supply disruptions. AI models respond to live inputs and recommend adjustments before congestion appears on the floor. That capability turns operations into an early‑warning system instead of a cost-center fire drill.
Labor costs rise each quarter, and attrition compounds onboarding expense. AI‑assisted scheduling matches skill sets and order profiles, filling shifts with the smallest possible headcount while respecting labor regulations. This shift keeps overtime low and morale high because staff see fair, consistent workloads. COOs who adopt these tools report smoother start‑of‑shift briefings and fewer late‑day surprises.
Investors now scan quarterly filings for technology initiatives that protect margins. Allocating budget toward AI initiatives in warehousing shows a direct link between innovation and earnings per share. Early adopters signal operational maturity to partners and customers, strengthening supply chain relationships. For these reasons, the use of AI in warehouse management sits near the top of every COO’s strategic agenda.
“Artificial intelligence now offers a route to accuracy that manual spreadsheets cannot match.”
7 ways AI is improving warehouse management for operations leaders
Warehouse tasks, once guided only by clipboards, now benefit from predictive insight and machine precision. AI technologies touch every step, from inbound scheduling to outbound routing, creating compounding productivity gains. Operations leaders who combine data, sensors, and software remove wasted travel, shrink safety stock, and shorten fulfillment cycles. Such gains turn fixed warehouse footprints into flexible profit centers.
1. AI forecasting improves inventory accuracy and reduces overhead
Forecast algorithms learn from years of order history, promotions, and even local weather to predict order volume with item‑level precision. This insight lets planners stock exactly what will move, trimming safety stock and freeing shelf space. Finance teams appreciate the lower working capital requirement, as cash is no longer tied up in slow‑moving pallets. Service levels rise because popular items rarely hit an out‑of‑stock status.
AI in warehouse management also connects forecasting with procurement queues, sending purchase orders automatically when models detect an upcoming shortfall. Suppliers receive steadier, earlier signals, which improves fill rates without last‑minute air shipments. When planners trust these predictions, they allocate effort to strategic supplier negotiations instead of chasing calls. The net effect is higher turnover, lower overhead, and a confident operations team.
2. Computer vision streamlines quality control and error reduction
High‑resolution cameras mounted above pack benches inspect every SKU in real time, catching label misprints and color mismatches that slip past the human eye. When a variance appears, the vision system flags the tote and alerts a supervisor through the warehouse management system. This immediate feedback stops flawed shipments before they reach the dock. Returns and credits fall, protecting both revenue and brand perception.
Unlike traditional sample auditing, computer vision inspects 100% of units without slowing throughput. Deep learning models continue to learn from new defect images, which sharpens detection accuracy week after week. Supervisors can review heat maps that pinpoint where errors begin, such as a misaligned printer or a damaged divider. Corrective action then focuses on root causes, not symptom chasing.
3. Autonomous robotics speed up order fulfillment with precision
Autonomous mobile robots (AMRs) ferry totes between storage aisles and pack stations, cutting unproductive walking for associates. Fleet software assigns paths that avoid congestion and recharge robots during natural lulls. Pickers stay in their zones and focus on accuracy rather than travel. Throughput climbs and floor injuries fall when heavy carts disappear.
Robots share telemetry with the warehouse execution platform, so planners see real‑time cycle counts and order status. When surge orders arise, the system summons idle robots or reroutes active ones without supervisor intervention. This fluid orchestration proves valuable during peak season, when traditional labor pools run thin. Capital outlay pays back quickly because labor hours per order fall and capacity scales when order volume surges.
4. Predictive maintenance helps prevent costly equipment downtime
Sensors on conveyors, sorters, and forklifts stream vibration, temperature, and power‑draw data into analytics engines. Machine learning models compare these readings against healthy baselines, flagging anomalies days before a bearing fails. Maintenance crews schedule repairs during planned pauses, avoiding emergency service calls. Uptime stability supports reliable service‑level agreements with carriers.
Cost savings extend beyond replacement parts. Predictive scheduling reduces overtime for mechanics and lowers rental expenses for backup equipment. Spare‑parts inventory also shrinks because planners know which components will be needed and when. Such clarity converts maintenance from a reactive cost center into a strategic safeguard.
5. AI-powered routing optimizes labor allocation in real time
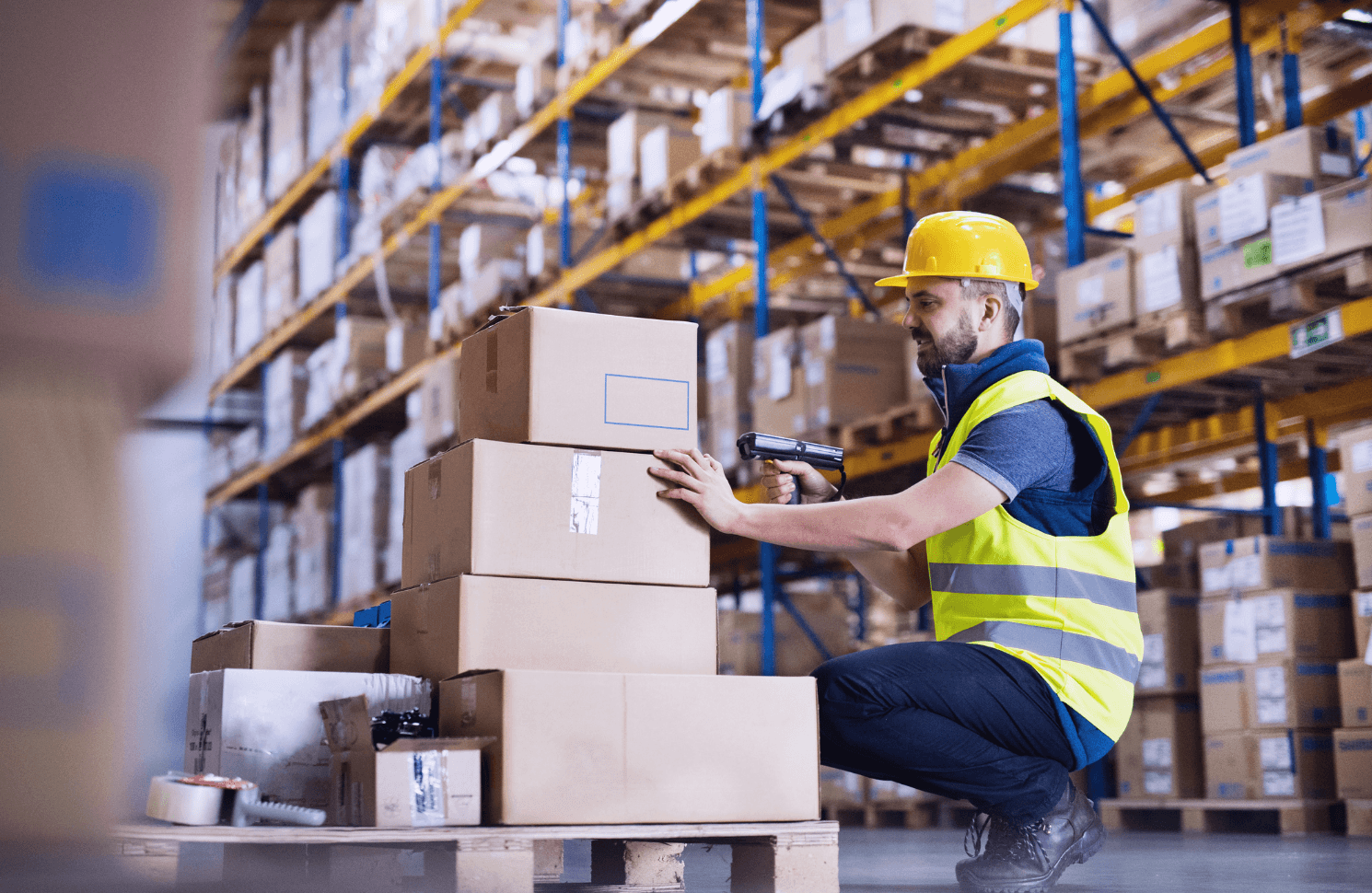
During each shift, thousands of variables shape workload: order size, aisle congestion, and operator skill sets. Routing algorithms assess these inputs every few seconds and direct pickers to the most efficient next task. Assignments adjust automatically when a rush order arrives or a forklift goes offline. Staff spend less time waiting for instructions and more time completing value‑added steps.
Supervisors watch an intuitive dashboard that highlights where staffing should flex. The system flags zones trending behind the goal so floaters can reinforce those areas before a bottleneck forms. Overtime drops because tasks finish within planned shift boundaries. Workers appreciate fair workload distribution, which improves retention.
6. Machine learning enhances picking and packing efficiency
Pattern‑recognition models review pick paths and identify sequence improvements that a human planner might miss. Re‑slotting suggestions group high‑velocity items near pack stations, slicing travel distance per order. Packing algorithms also recommend carton sizes, reducing dunnage and freight costs. The result is faster lines and lighter shipments.
As the use of AI in warehouse management matures, adaptive algorithms retrain nightly to reflect new SKUs and volume shifts. Operations teams no longer wait for quarterly engineering reviews to see process gains. Continuous micro‑optimizations compound into significant annual savings. That agile improvement loop gives COOs confidence in hitting service and cost targets.
7. AI insights improve procurement and supply chain decisions
When forecasting, routing, and quality data roll up into a unified analytics stack, leaders gain a panoramic view of spend and performance. Procurement specialists can spot when a supplier trend hints at late shipments or rising defect rates. AI models recommend alternative vendors, cross‑dock options, or earlier cut‑off times based on probability scores. These foresight tools reduce stock‑outs and help negotiate favorable contract terms.
Finance teams feed those insights into cash‑flow planning, aligning inventory purchases with revenue timing. With fewer emergency shipments, transportation costs stabilize, and carbon‑emission targets meet compliance thresholds. Executive dashboards translate complex analytics into digestible visuals that support quick course corrections during board reviews. Supply chains that react hours sooner than competitors build loyalty among retailers and consumers alike.
AI no longer sits in the lab; it runs forklifts, cameras, and cloud dashboards inside leading warehouses. Leaders who integrate these tools see freight leaving sooner, returns shrinking, and profit expanding. Each capability also feeds the next, creating a flywheel of data and improvement. Early movers set a high bar that late adopters will struggle to match.
"Continuous micro-optimizations compound into significant annual savings.”
How to evaluate the use of AI in warehouse management systems
Selecting an AI‑ready platform requires a balance of technical fit and financial return. Assessing the use of AI in warehouse management also involves cultural readiness and support from floor supervisors. Clear criteria keep projects on schedule and prevent scope creep. Documented expectations give all stakeholders a shared view of what success looks like.
- Data compatibility: Confirm that the platform ingests structured and unstructured records from scanners, ERP feeds, and IoT sensors without extra middleware. Clean data at the source speeds model training and avoids costly rework.
- Integration effort: Assess available APIs and pre‑built connectors for your warehouse execution system, robotics fleet manager, and procurement suite. Fewer custom scripts translate into quicker time to value.
- Model transparency: Insist on dashboards that show feature importance and prediction confidence. Clear visibility helps supervisors trust recommendations and adopt them in daily routines.
- Security posture: Review the vendor’s SOC 2 attestation, encryption approach, and role‑based access controls. Strong safeguards protect both proprietary processes and customer data.
- Scalability limits: Stress‑test the system with peak‑season order volumes in a sandbox instance. Results reveal how processing latency and licensing costs grow as usage climbs.
- Support structure: Identify named resources for implementation, training, and ongoing model tuning. A dedicated success manager shortens issue resolution time.
- Business metrics linkage: Tie each feature to a financial KPI such as labor cost per order or on‑time ship rate. Stakeholders are more likely to approve funding when benefits appear in familiar scorecards.
Disciplined evaluation removes emotion from purchase decisions. Teams that map capabilities to measurable targets spot gaps early and negotiate fixes before contracts finalize. That preparation also smooths change management with frontline employees. A strong selection process sets the stage for compounding gains once the system goes live.
How Lumenalta helps COOs drive efficiency through warehouse AI

Lumenalta pairs warehouse data architects with operations specialists to frame use cases that cut cycle time without disrupting ongoing service. Our team installs edge collectors that pull scanner, conveyor, and robot telemetry into a single event stream within weeks, not quarters. Pre‑trained forecasting and routing models then bring immediate accuracy, while an API layer dovetails with major warehouse management systems to keep IT overhead low. You receive dashboards that link every recommendation to labor spend, cubic utilization, and ship‑on‑time rate, so results show up in board reports. Weekly sprints let you refine targets as conditions shift, creating a cadence that operations staff understand and support.
Beyond algorithms, we focus on skill transfer. Co‑working sessions train supervisors to interpret variance alerts and adjust workflows with confidence instead of escalating tickets. Our security team aligns settings with corporate policies, covering encryption, audit logging, and role controls from day one. Post‑launch reviews quantify savings and feed the investment story that finance requires for future expansions. That cycle of evidence builds trust, proving that technology decisions safeguard margins and strengthen supply resilience.
Lumenalta stands as a steady partner, committed to measurable outcomes that let COOs lead with certainty.
table-of-contents
- Why AI in warehouse management is a priority for COOs
- 7 ways AI is improving warehouse management for operations leaders
- 1. AI forecasting improves inventory accuracy and reduces overhead
- 2. Computer vision streamlines quality control and error reduction
- 3. Autonomous robotics speed up order fulfillment with precision
- 4. Predictive maintenance helps prevent costly equipment downtime
- 5. AI-powered routing optimizes labor allocation in real time
- 6. Machine learning enhances picking and packing efficiency
- 7. AI insights improve procurement and supply chain decisions
- How to evaluate the use of AI in warehouse management systems
- How Lumenalta helps COOs drive efficiency through warehouse AI
- Common questions about AI in warehouse management
Common questions about AI in warehouse management
How can I use AI to reduce warehouse costs without major infrastructure changes?
What AI use cases offer the fastest ROI in warehouse operations?
Is AI in warehouse management scalable for seasonal demand spikes?
How do I know if my data is ready for warehouse AI tools?
Can warehouse AI improve supply chain coordination beyond my four walls?
Want to learn how artificial intelligence can bring more transparency and trust to your operations?