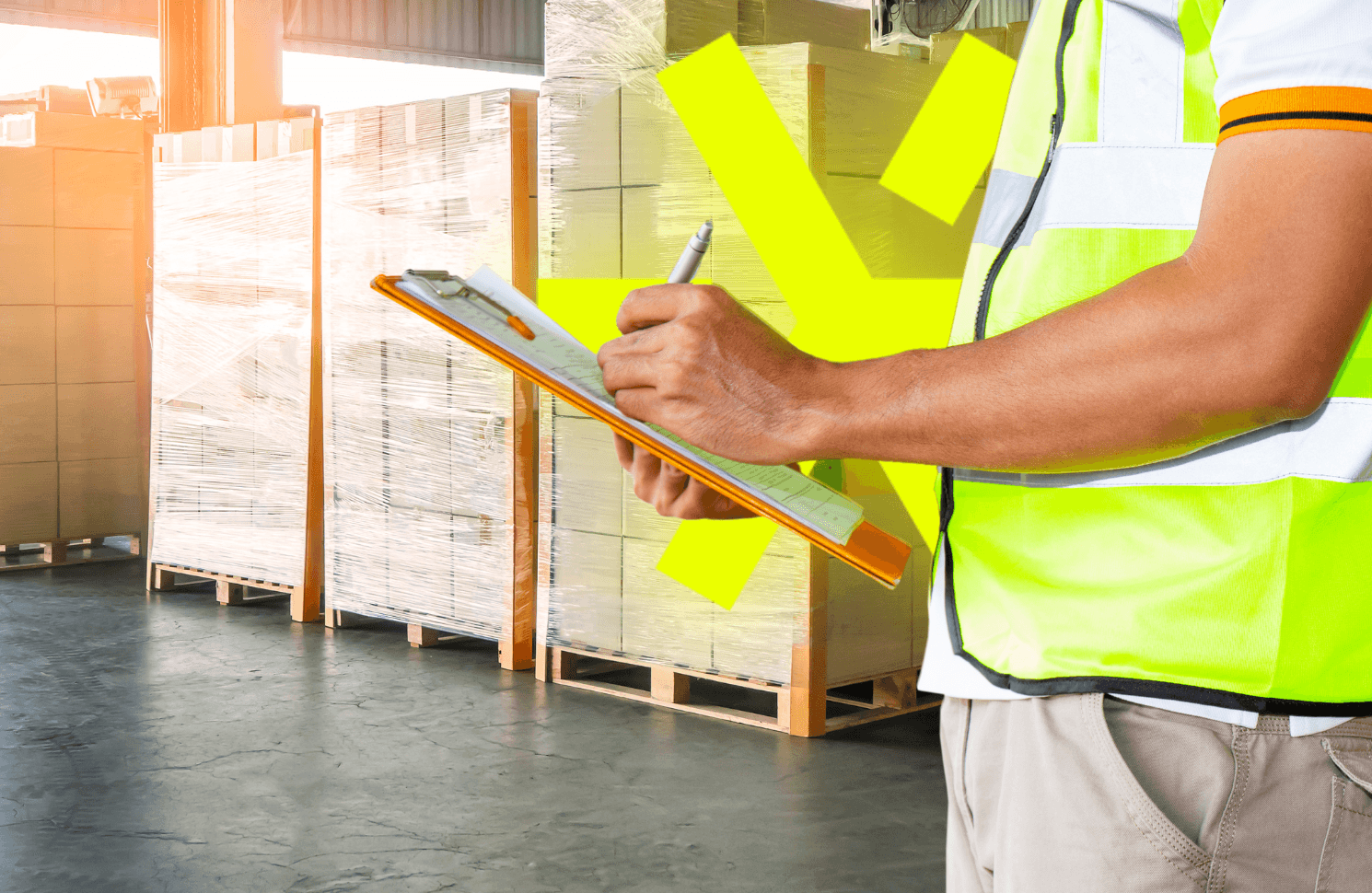
Why siloed warehouse systems are quietly draining profitability
JUN. 30, 2025
3 Min Read
When your warehouse data lives in silos, every decision slows to a crawl and hidden costs pile up.
Key takeaways
- 1. Data silos between WMS, TMS, and ERP systems slow every business-critical decision in warehouse operations.
- 2. Fragmented systems introduce costly inefficiencies including manual rework, inventory errors, and fulfillment delays.
- 3. Real-time visibility across platforms isn’t optional—it’s a requirement for profitability and operational control.
- 4. Unified data enables faster action, more accurate forecasting, and better labor allocation without adding IT complexity.
- 5. Warehouse leaders who act in real time improve margins, reduce maintenance costs, and drive measurable results.
Fragmented systems mean each shift, each order, and each inventory count depends on manual reconciliation and guesswork. For example, one study found knowledge workers spend an average of 12 hours per week “chasing data”. That’s time wasted on pulling together fragmented reports instead of improving processes. In warehousing, this inefficiency translates directly into missed sales and higher labor costs. Inefficient supply chain and inventory management worldwide already cost companies more than $1.8 trillion annually. When WMS, TMS, and ERP systems can’t share data, the business loses visibility into stock levels, order status, and shipments. CIOs lose the real-time insight needed to optimize fulfillment, causing delayed shipments and frustrated customers. In fact, 75% of supply chain leaders rely on 3–10 different systems just to make basic decisions, yet over half still struggle with critical blind spots. In this context, delayed decisions are far more damaging than slow dashboards. Every hour spent reconciling siloed data pushes critical fixes and optimizations into the future, eroding margins and accuracy in the meantime.
“When your warehouse data lives in silos, every decision slows to a crawl and hidden costs pile up.”
Data silos in the warehouse are delaying every decision that matters
Data trapped in separate systems creates blind spots that throttle throughput. When inventory updates from your WMS don’t flow into the ERP, leaders can’t see which products are on the shelves or on order. When your TMS can’t share shipment statuses with the WMS, no one knows which orders are late until customers complain. These disconnections force teams into time-consuming workarounds. Employees spend hours cross-checking spreadsheets and calling colleagues, instead of executing on the floor. The result is that routine tasks become bottlenecked: daily inventory counts take days, labor can’t be allocated efficiently, and by the time the office uncovers a stockout or bottleneck, it’s already too late.
In a fractured data environment, decision-making shrinks to fighting fires instead of preventing them. Leaders end up trusting outdated reports rather than real-time signals. This lost visibility isn’t theoretical. Data silos can cost businesses up to 30% of potential annual revenue. Put simply, when teams wait for fragmented reports, every corrective action is delayed, from reordering popular products to rerouting shipments. The true cost of that delay is not just extra manual labor – it’s lost sales, higher carrying costs, and unhappy customers. The message for CIOs is clear: if your systems aren’t sharing data automatically, you’re essentially throwing away profit with every delayed decision.
Unify your WMS, TMS, and ERP data into a single source of truth.
Fragmented systems lead to more than just operational inefficiency
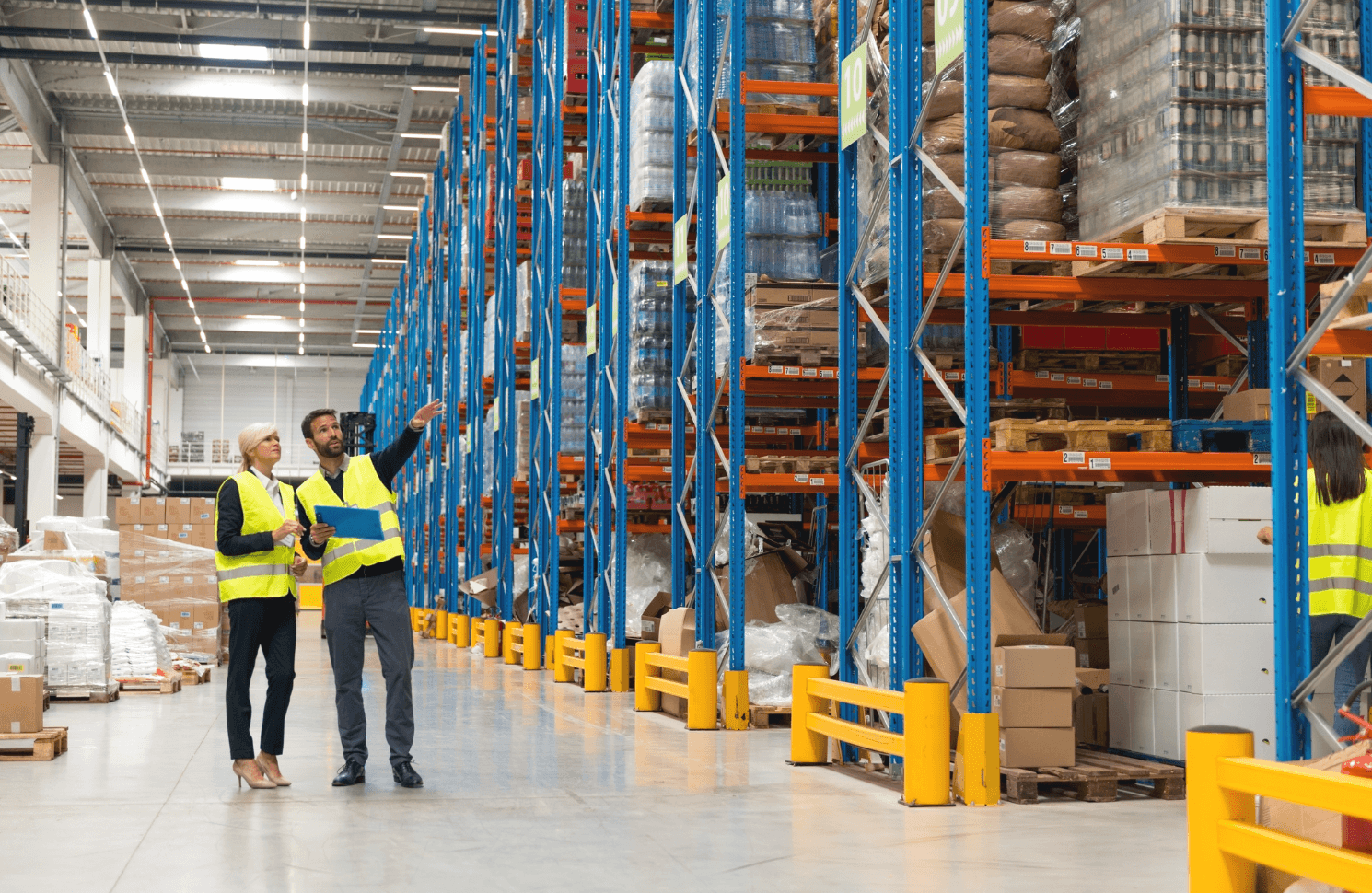
When WMS, TMS, and ERP data don’t flow together, the consequences ripple far beyond slow processes. The hidden costs show up in many unexpected places. The list below highlights key pain points created by disconnected warehouse systems:
- Inventory inaccuracies: Mismatched data causes stock counts to be incorrect. One system may show an item in stock while another has already shipped it, leading to overstock or stockouts. This wastes money on excess inventory and frustrates customers with delays.
- Order fulfillment delays: Without up-to-the-minute updates, orders slip through the cracks. Picking and shipping errors increase when the WMS isn’t aligned with sales orders or shipping schedules. Every mistaken shipment or missed delivery date eats into customer trust and profit.
- Excess labor and overtime: Teams spend hours on manual data entry and reconciliation. Workers stop picking and start hunting for information, or supervisors work nights to correct errors. This overtime inflates payroll and diverts staff from value-added work.
- Higher IT overhead: Maintaining multiple incompatible systems is expensive. IT teams spend months patching integrations, upgrading outdated software, and dealing with endless error reports. These maintenance costs add up year after year without improving operations.
- Missed revenue opportunities: Fragmented data means leadership acts on partial information. Pricing, promotions, and sourcing decisions suffer when executives don’t see the full picture. This leads to conservative choices, missed upsell chances, and ultimately lower sales growth.
- Decision Bottlenecks: Disconnected systems force leaders into a reactive mode. Every time a problem arises, like a shipment delay, a sudden shortage, managers must wait for reports or hunt down experts. This slows every business decision, from staffing plans to new product launches.
Each of these issues costs money in different ways – whether in wasted labor, expediting charges, or lost sales. Together, they can easily drain about 30% of a business’s revenue potential. Even “small” problems like a single day’s delay in knowing inventory levels can ripple into huge financial losses over a year. In sum, siloed systems are a tax on every part of warehouse operations. Breaking down these silos isn’t just about efficiency, but about preserving profitability.
Unified data across WMS, TMS, and ERP isn’t optional—it’s urgent
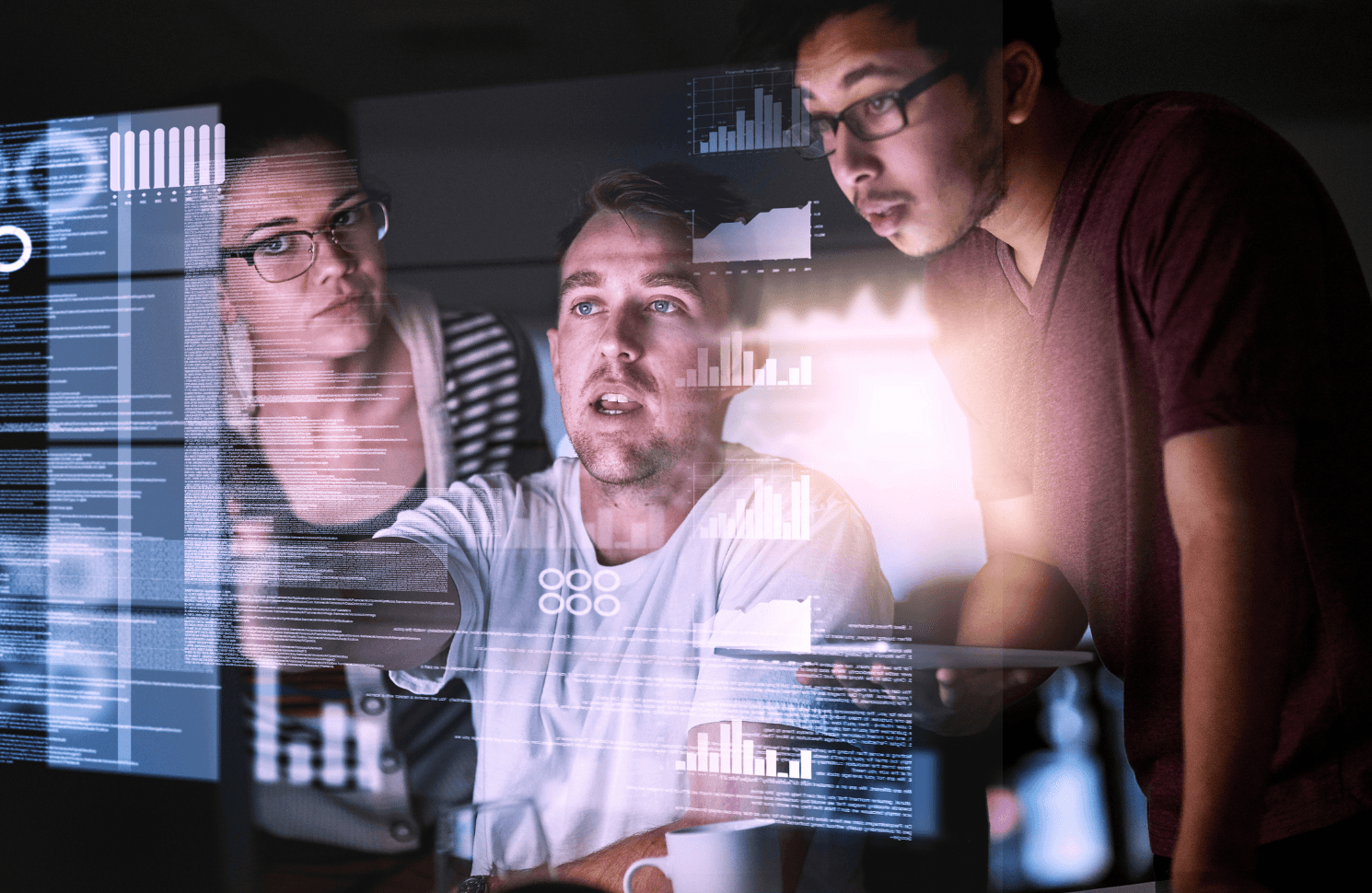
Connecting data from all warehouse systems is now a business imperative, not a nice-to-have. A unified data view means warehouse leaders gain a single source of truth, enabling faster, smarter decisions.
Single source of truth
Imagine having a dashboard that reflects every pick, pack, and pallet movement as it happens. With integration, each WMS scan updates the ERP inventory and triggers a shipping update in the TMS instantly. This single view eliminates guessing. You always know exactly how many units are available, where they are, and which orders are on the way. A single source of truth keeps KPIs reliable and builds trust in the data. When numbers from one system always match those in another, managers can confidently allocate stock and labor.
Accelerated decision-making
The moment data flows automatically, decision cycles compress. Instead of waiting for daily or weekly reports, you get alerts in real time. For example, as soon as a high-priority order is picked and packed, finance and operations are immediately informed and can pre-emptively prepare the shipment. Forecasts and reorder triggers use live data, so restocks and production plans stay ahead of demand. This agility translates directly into speed to market. Warehouses that fully automate their data pipelines see big efficiency gains. One industry report notes warehouse automation can boost productivity by ~25% and improve stock-use efficiency by 30%. Those kinds of improvements are only possible when the underlying data is clean and integrated.
Reduced costs and higher margins
Unified data cuts waste from warehouse operations. When every transaction feeds into one system, duplicate entries vanish and error rates plummet. There’s no longer a need for extra checks or reconciliations, freeing staff for higher-value tasks. IT budgets shrink too, since you maintain one integrated platform instead of patching together siloed applications. Over time, this simplification has a major impact on the bottom line. Lower overhead and fewer errors mean higher margins. In addition, leaders can reduce excess safety stock. With real-time visibility, stock levels remain lean without risking stockouts. The result: significant inventory carrying cost savings.
Unlocking untapped potential
Finally, unified data fuels better strategy. With all warehouse, transport, and ERP data in sync, analytics can uncover opportunities hidden in the numbers. Leaders can pinpoint the most profitable product lines, anticipate bottlenecks before they occur, and adjust labor dynamically around peak hours. This data-driven agility means the warehouse becomes a growth engine, not just a cost center. In short, integrating WMS, TMS, and ERP data gives CIOs the platform to innovate, capturing revenue that siloed systems simply waste away.
“Unified data fuels better strategy—analytics can uncover opportunities hidden in the numbers.”
Warehouse leaders must act in real time, not in hindsight
Warehouse leadership today means responding to events the moment they happen. When data is integrated and accessible, managers move from firefighting old problems to preventing new ones. Real-time inventory tracking lets you adjust labor and space on the fly. For instance, adding pickers the second a big order comes in. Live shipment feeds let logistics teams reroute carriers immediately if delays arise, rather than patching problems after they pile up. Forecasting becomes predictive: you use current sales trends to tweak replenishment in real-time, avoiding stockouts before they impact revenue.
You also empower teams across functions. Purchasers negotiate better terms when they know what’s truly selling and what isn’t. Customer service can provide accurate ETAs when order data is updated live. In short, every stakeholder benefits when decisions are based on current facts instead of outdated snapshots. Imagine a CIO walking into a meeting and, instead of tense guessing, pointing to a unified dashboard showing current throughput, fulfillment rates, and risk alerts – all in one place. That kind of visibility lets you coordinate IT, operations, and finance around what matters now.
Shifting to real-time operations requires clear priorities, the right tools, and stakeholder alignment. Yet the rewards are concrete: faster fulfillment, happier customers, and measurable gains in return on investment. Acting in real time is no longer a technical exercise; it’s how warehouse leaders preserve margins and competitive edge. If you wait to fix errors tomorrow, those lost hours today are revenue that can’t be recovered.
Lumenalta’s approach to unified warehouse data
Warehouse leaders who must act now instead of later need a partner to make it happen. Lumenalta’s approach connects WMS, TMS, and ERP into one real-time data ecosystem. This unified platform automatically synchronizes transactions across systems so that every stakeholder sees the same up-to-date information at once.
By doing this, we eliminate the manual tie-ups and blind spots that slow fulfillment. CIOs see immediate improvements: faster cycle times, fewer stockouts and overstocks, and a dramatic drop in time spent reconciling data. The solution is designed to scale with the business, cutting IT maintenance overhead so teams can focus on innovation instead of firefighting. In practice, this means a single source of truth drives everyday operations. Warehouse managers can reassign labor or reroute shipments on the fly because they trust the live data. Inventory planners eliminate guesswork and cut carrying costs by ordering only what’s needed.
Table of contents
- Data silos in the warehouse are delaying every decision that matters
- Fragmented systems lead to more than just operational inefficiency
- Unified data across WMS TMS and ERP isn’t optional it’s urgent
- Warehouse leaders must act in real time not in hindsight
- Why Lumenalta delivers the unified warehouse visibility CIOs need
- Common questions
Common questions
How do data silos impact warehouse profitability?
What are the signs that my warehouse data is siloed?
Why does real-time warehouse data matter for CIOs?
Can I unify warehouse data without replacing all my systems?
How does unified data improve my fulfillment speed?
Unify your WMS, TMS, and ERP data into a single source of truth.