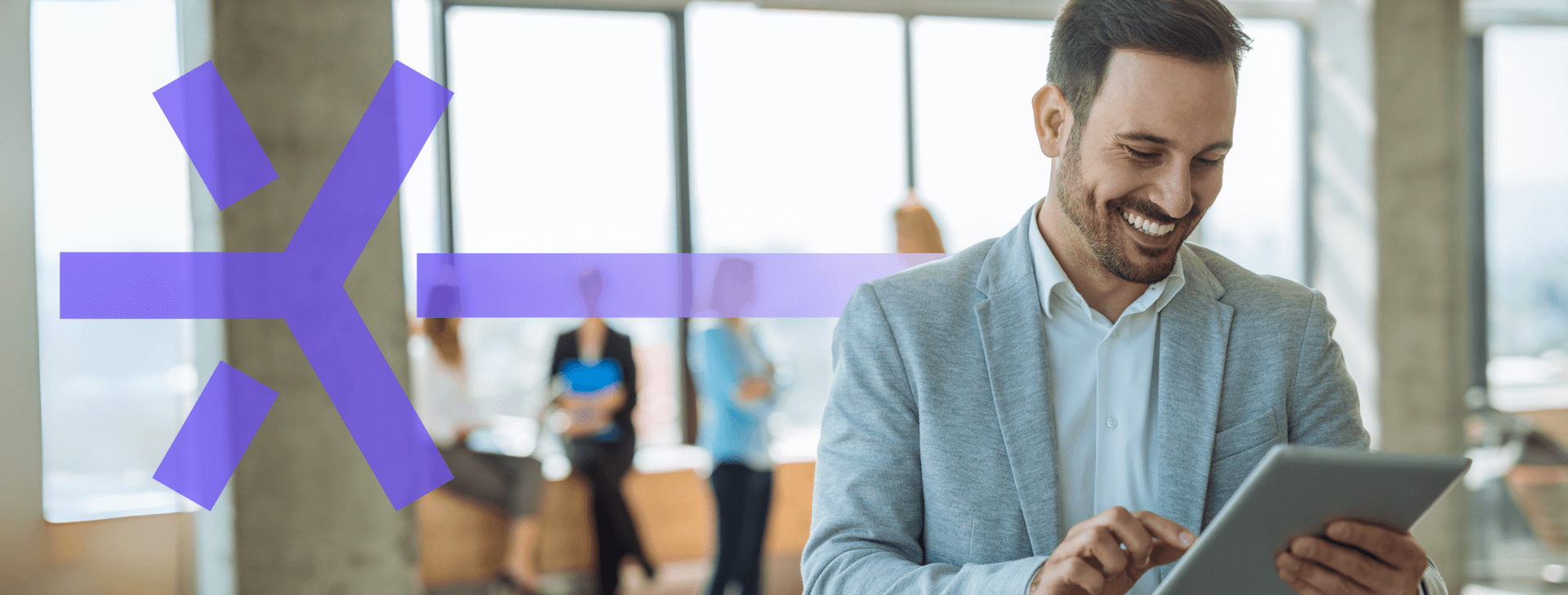
How CTOs can lead digital transformation across the extended supply chain
MAY. 21, 2025
4 Min Read
Every missed shipment now ripples outward, cutting margins and bruising brand reputation in minutes.
Supply chain leaders see that small process gaps scale across partner networks, putting strategic goals at risk. Technology chiefs addressing these gaps must push beyond isolated upgrades and instead guide a full digital transformation in the supply chain. Strengthening data flow, governance, and collaboration across every node ultimately determines how quickly new revenue streams emerge.
key-takeaways
- 1. Digital threads linking every partner turn fragmented operations into a single data source of truth that supports faster decisions.
- 2. CTOs and COOs overcome transformation hurdles by ranking projects on cash impact, simplifying data foundations, and embedding change leadership early.
- 3. Benefits such as lower freight spend, higher forecast precision, and stronger ESG reporting compound because each win feeds new insights.
- 4. Common pitfalls, including data silos, vendor lock‑in, and skills gaps—require clear ownership and outcome‑based KPIs to resolve.
- 5. Lumenalta accelerates progress with iterative sprints, cloud‑native tooling, and governance frameworks that deliver measurable financial returns.
Why digital transformation in the supply chain matters now more than ever
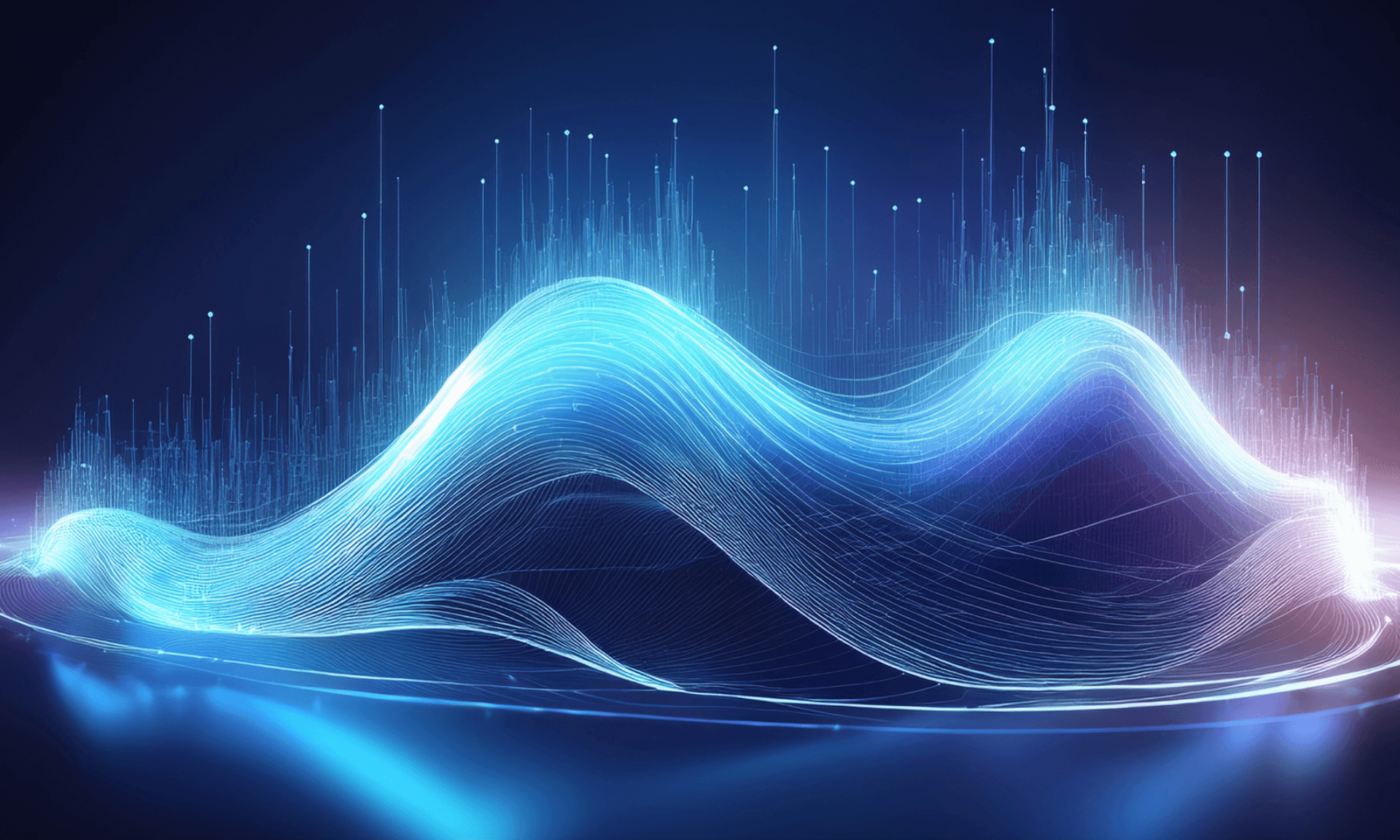
Global volatility, fluctuating freight costs, and rising customer expectations have exposed brittle links from tier‑n suppliers to last‑mile carriers. Manual processes hide root‑cause delays, and siloed systems distort true landed cost. A unified digital thread replaces those blind spots with data that tells a single story, letting executives pinpoint interventions before issues compound.
Modern analytics also shrinks the gulf between planning and execution. Predictive inventory buffers adapt to real‑time demand, and exception‑based workflows free planners from routine approvals. This agility explains why digital transformation of the supply chain is important for protecting margins and safeguarding growth.
“A unified digital thread replaces blind spots with data that tells a single story, letting executives pinpoint interventions before issues compound.”
Understanding digital transformation across the extended supply chain
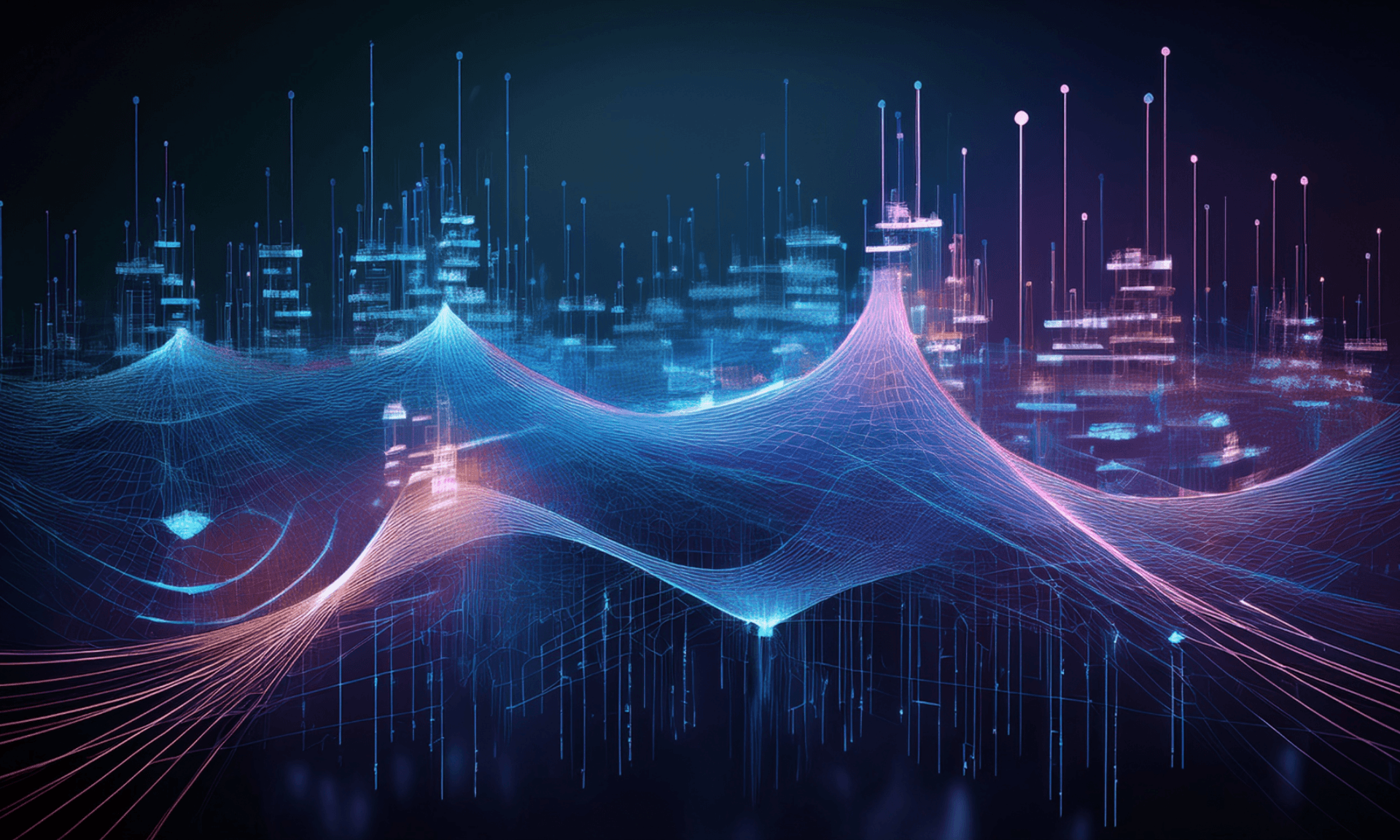
Supply chain modernization stretches well beyond warehouse automation. Digital threads now link suppliers, carriers, and customers into one data‑rich network. Understanding how each layer contributes to service, cost, and resilience defines the first step.
Real‑time visibility across Tier‑N suppliers
Sequenced production plans falter when a sub‑component stalls two tiers back. Cloud‑based portals feed shipment status, quality certificates, and capacity signals into a shared control tower. Early alerts let procurement switch allocations before the factory line slows. Resilience improves without ballooning safety stock.
Connected logistics orchestration
Ports, rail yards, and trucking fleets often run separate platform stacks. API‑centric integration shares tracking, dwell, and customs clearance milestones in real time. Route planners spot detention risks early and rebalance loads across modes. On‑time delivery metrics climb while demurrage fees fall.
Sensor‑driven warehouse execution
Internet of Things (IoT) tags monitor temperature, shock, and humidity throughout storage zones. Machine‑learning models flag cartons nearing threshold limits so teams adjust pick paths on the fly. The result is fewer spoilage claims and higher recalled‑unit traceability.
Collaborative demand shaping
Point‑of‑sale feeds, marketing campaigns, and social sentiment roll into a unified demand signal. Suppliers receive confirmed forecasts instead of aspirational spreadsheets, shrinking order‑to‑cash cycles. Inventory turns to improve, and markdowns decline.
Governance and security at scale
Data flowing across external partners raises compliance exposure. Zero‑trust controls, tokenized identifiers, and audit automation satisfy trade laws and industry regulations without slowing throughput. Stakeholder confidence rises as error‑prone manual reconciliations fade.
Digital collaboration only works when each contributor trusts the data and the process. Precise governance, consistent metrics, and shared incentives keep every node aligned. Most of all, executives gain a single version of the truth that accelerates decision cycles and compresses costs.
How CTOs and COOs can address supply chain digital transformation challenges
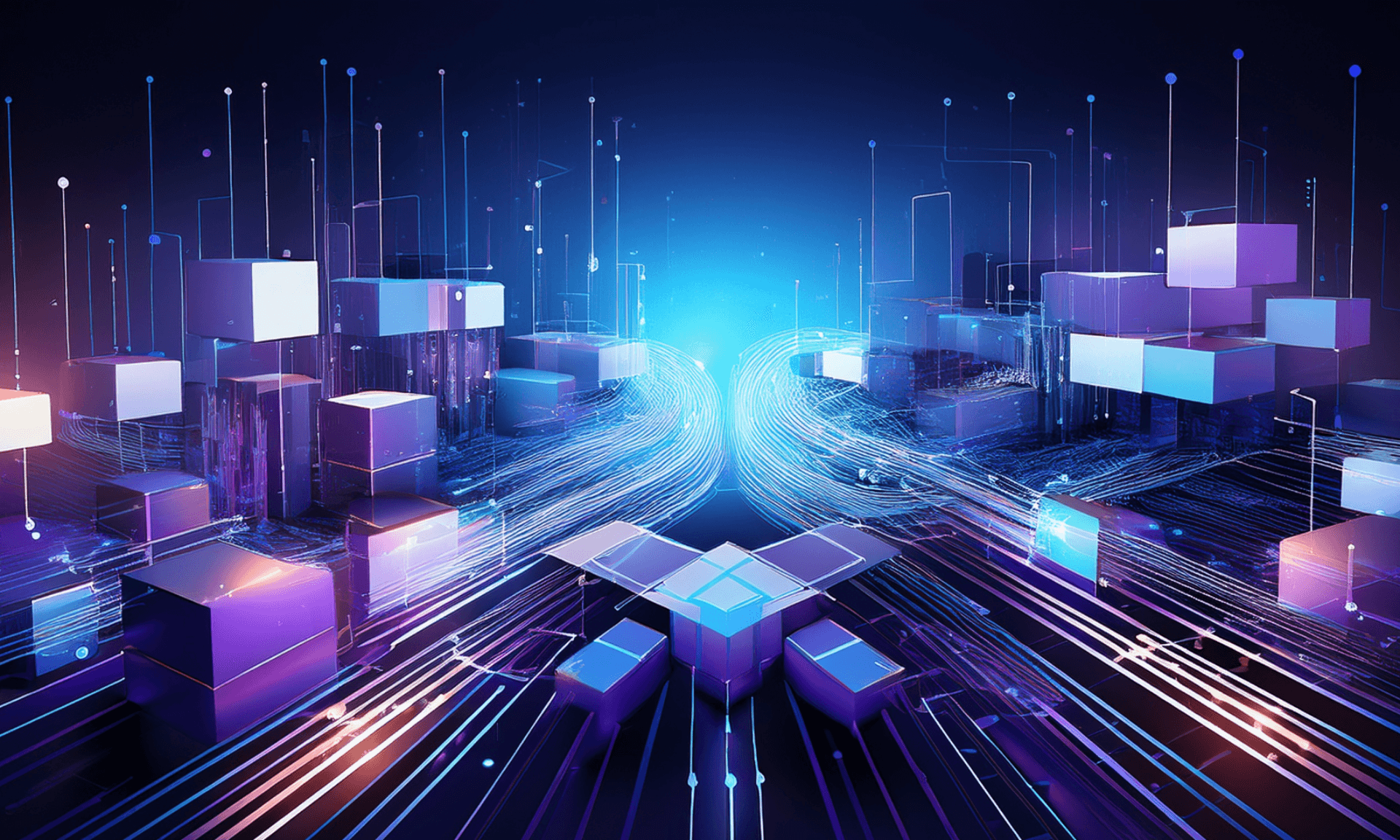
Budget constraints, siloed mindsets, and legacy architectures frustrate many digitization roadmaps. Successful leaders combat these barriers with a targeted playbook that aligns with technology, process, and culture. A clear operating model keeps progress measurable and momentum visible.
Prioritize use cases by financial impact
Not every automation delivers equal value. Leaders rank programs using hard metrics such as cash‑to‑cash cycle time and expedited freight cost. Funding flows to initiatives that move the needle within two quarters, building credibility for larger bets.
Simplify the data foundation
Multiple ERPs, transport systems, and shop‑floor assets spawn conflicting master data. A canonical data model—wrapped with automated quality checks—lets analytics compare apples to apples. Teams spend less time cleansing spreadsheets and more time improving service metrics.
Integrate change management early
Operators resist new workflows when training arrives late. Embedding frontline leads in design workshops uncovers practical constraints and boosts adoption. Clear win stories circulate across geographies, reinforcing enthusiasm.
Align cybersecurity with operational targets
Factory networks and logistics partners present an expanding attack surface. Security architects map vulnerabilities to business continuity scenarios, then deploy micro‑segmentation and continuous monitoring. Board‑level dashboards connect risk posture to shipment reliability.
Measure progress with outcome‑based KPIs
Traditional IT milestones focus on go‑live dates. Supply chain transformation instead tracks on‑time performance, freight cost per unit, and forecast accuracy. Regular scorecard reviews let executives adjust course quickly, avoiding sunk‑cost surprises.
Early wins create self‑funding momentum that attracts cross‑functional backing. Structured communication, disciplined metrics, and a relentless focus on cash impact give CTOs and COOs the influence required to overcome entrenched habits. The result is a scalable foundation that adapts as market conditions shift.
“Early wins create self‑funding momentum that attracts cross‑functional backing.”
Want to learn how digital transformation can bring more transparency and trust to your operations?
Key benefits of digital transformation in logistics and supply chain operations
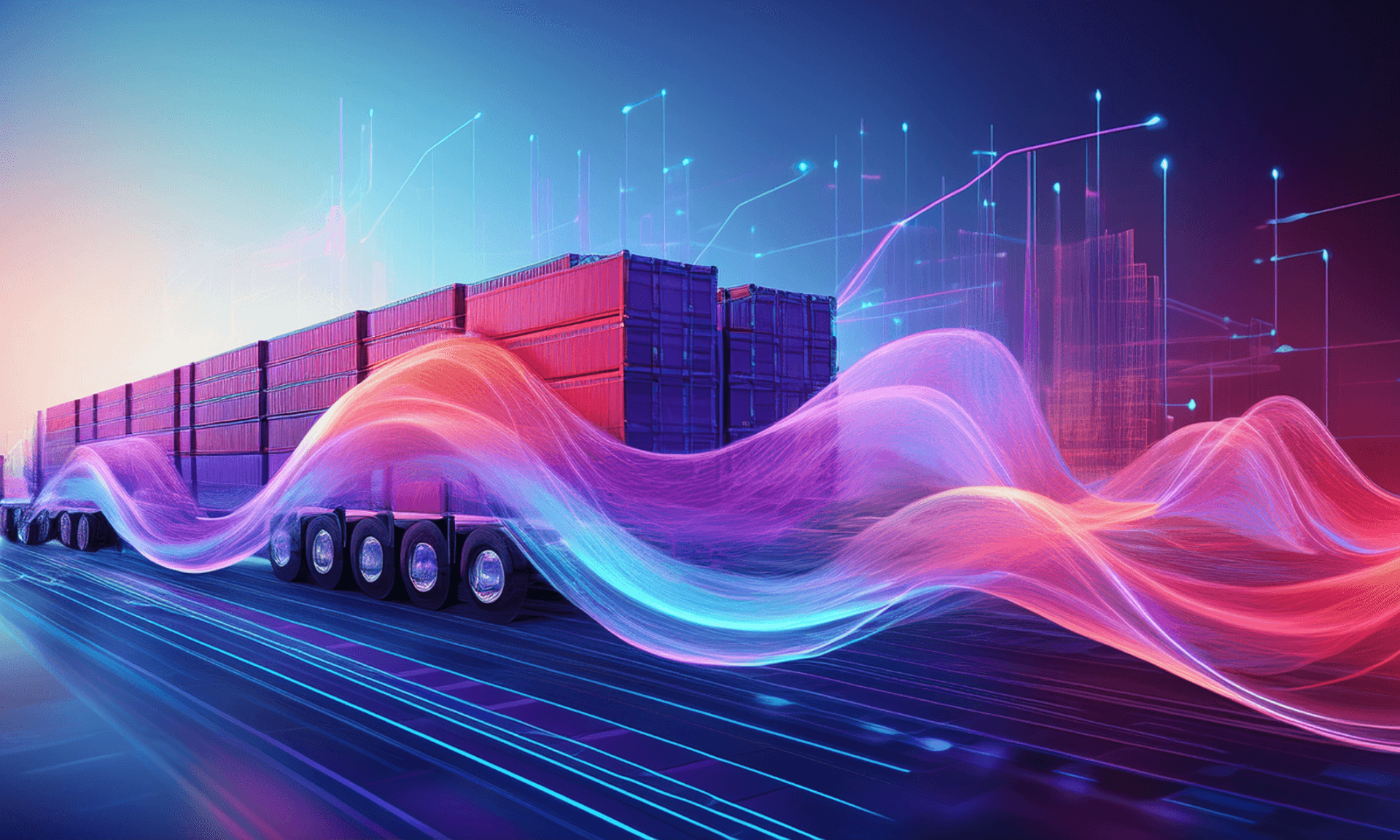
Supply chain executives face constant pressure to increase speed, reduce costs, and limit exposure to disruptions. Digital advancements allow decision-makers to improve control without adding headcount or overhead. Each capability works together to unlock efficiency, transparency, and value across every node.
- Faster order cycles: Automated procure‑to‑pay workflows cut manual touchpoints and free working capital sooner.
- Lower freight spend: AI‑guided mode selection and load consolidation shrink premium shipping charges.
- Higher forecast precision: Machine learning blends weather, promotions, and macro indicators, trimming stock‑outs and obsolescence.
- Improved supplier scorecards: Shared dashboards spotlight OTIF (on‑time in‑full) trends, prompting corrective action before penalties accrue.
- Stronger ESG performance: Digital emissions tracking links route decisions to carbon impact, supporting regulatory disclosures.
- Resilient capacity: Digital twin simulations test disruption scenarios, revealing cost‑effective mitigation strategies.
Tactical improvements grow stronger when supported by accurate, real-time data and scalable processes. The financial and operational upside compounds quickly as insights drive better execution. Executives who act now secure gains that strengthen market position and investor confidence.
Common digital transformation challenges in supply chain management
Misalignment between business goals and IT capabilities often delays supply chain modernization efforts. Challenges surface when core processes are too rigid, disconnected, or poorly governed across partner ecosystems. Long-term success depends on diagnosing these blockers early and structuring a clear path around them.
- Data silos: Disparate point solutions lock crucial metrics in proprietary formats, obstructing end‑to‑end insight.
- Legacy technical debt: Outdated middleware cannot process streaming IoT data or scale with cloud‑native analytics engines.
- Fragmented ownership: No single role holds authority across planning, sourcing, manufacturing, and logistics, delaying cross‑functional decisions.
- Change fatigue: Successive tool rollouts tire frontline staff and erode trust in new initiatives.
- Vendor lock‑in: Rigid commercial terms with incumbent providers inhibit cost‑effective experimentation.
- Skills gap: Teams lack architects fluent in both operations and modern integration patterns.
Addressing these challenges upfront increases adoption, reduces delivery risk, and protects long-term returns on investment. Programs succeed when there is clarity in sponsorship, accountability, and outcome measurement. Strong executive alignment turns these common pitfalls into manageable course corrections.
The current and future state of digital supply chain transformation
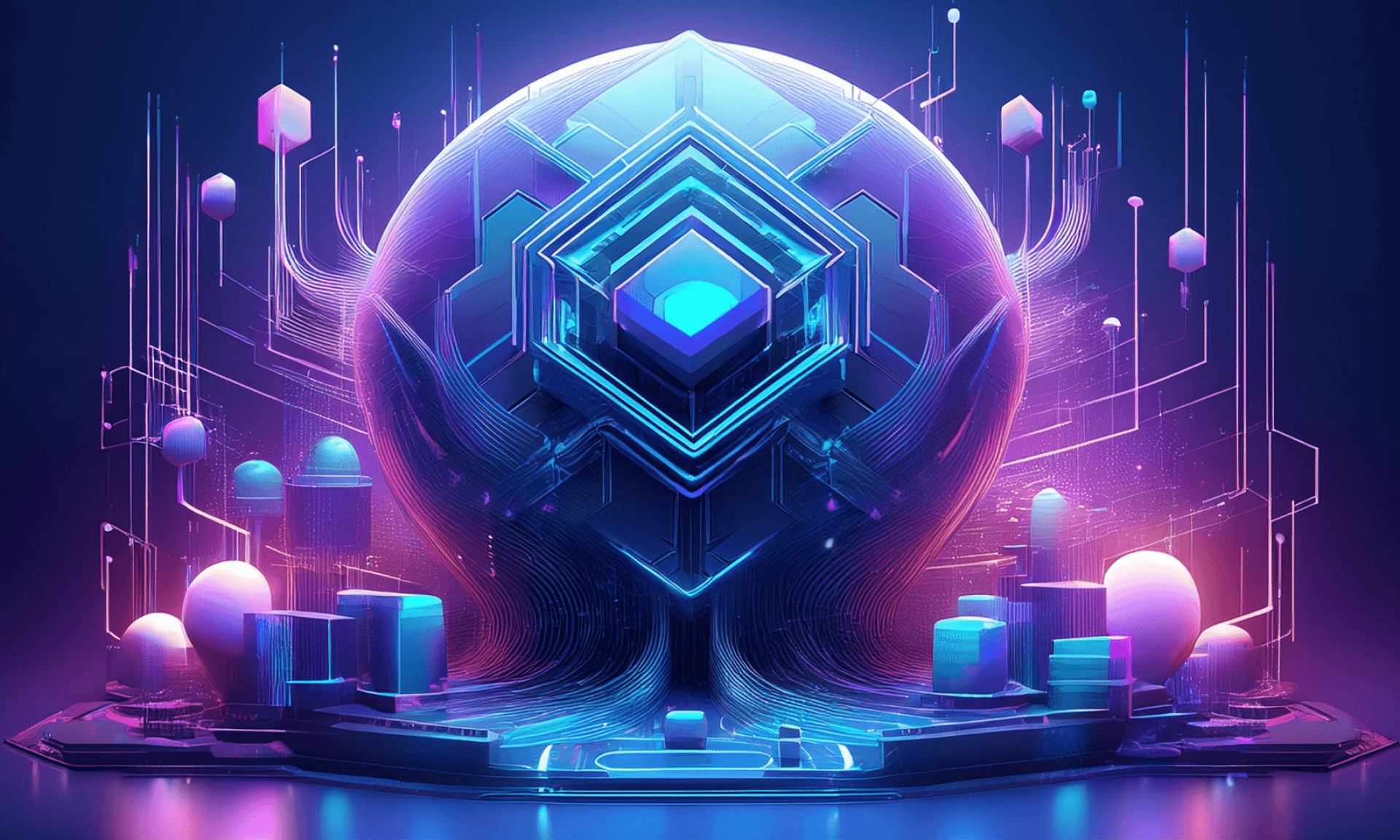
Supply chain technology reached an inflection point where cloud‑based composability meets advanced analytics. Investment priorities now center on real‑time data orchestration, resilience modeling, and sustainable operations. Understanding the trajectory clarifies which capabilities deserve attention today.
AI‑assisted planning
Generative algorithms propose demand forecasts with confidence intervals, summarizing causal drivers in plain language for planners. Scenario engines then optimize production, logistics, and inventory simultaneously. Performance reviews shift from retrospective variance analysis to proactive exception handling.
Autonomous logistics execution
Driver alerts, dock scheduling, and yard movements now use computer vision and telematics to self‑adjust schedules. When traffic snarls threaten service levels, orchestration engines reassign carriers without human intervention. Continuous feedback trims dwell and detention costs.
Circular supply considerations
Take‑back programs and refurbished product loops add reverse logistics complexity. Digital material passports track component lineage, guiding dismantling workflows and secondary market pricing. Sustainability goals move from glossy reports to shipment‑level measurements.
Quantum‑inspired optimization pilots
Large network design problems exceed classical solver limits. Quantum annealing techniques test trillions of route and capacity permutations to uncover lower cost‑to‑serve models. Early adopters report double‑digit freight savings on complex lane portfolios.
Federated data collaboration
Privacy regulations restrict raw data exchange with partners. Secure enclaves allow shared model training without revealing sensitive records. Forecast accuracy rises while compliance teams avoid regulatory penalties.
The current and future state of digital supply chain transformation rewards organizations that invest in adaptable architectures and data governance. Technology roadmaps must remain modular so emerging tools slot into place without wholesale rewrites. Leaders securing this foundation gain the agility to outpace disruption and capture new markets.
How Lumenalta helps drive digital transformation supply chain management goals
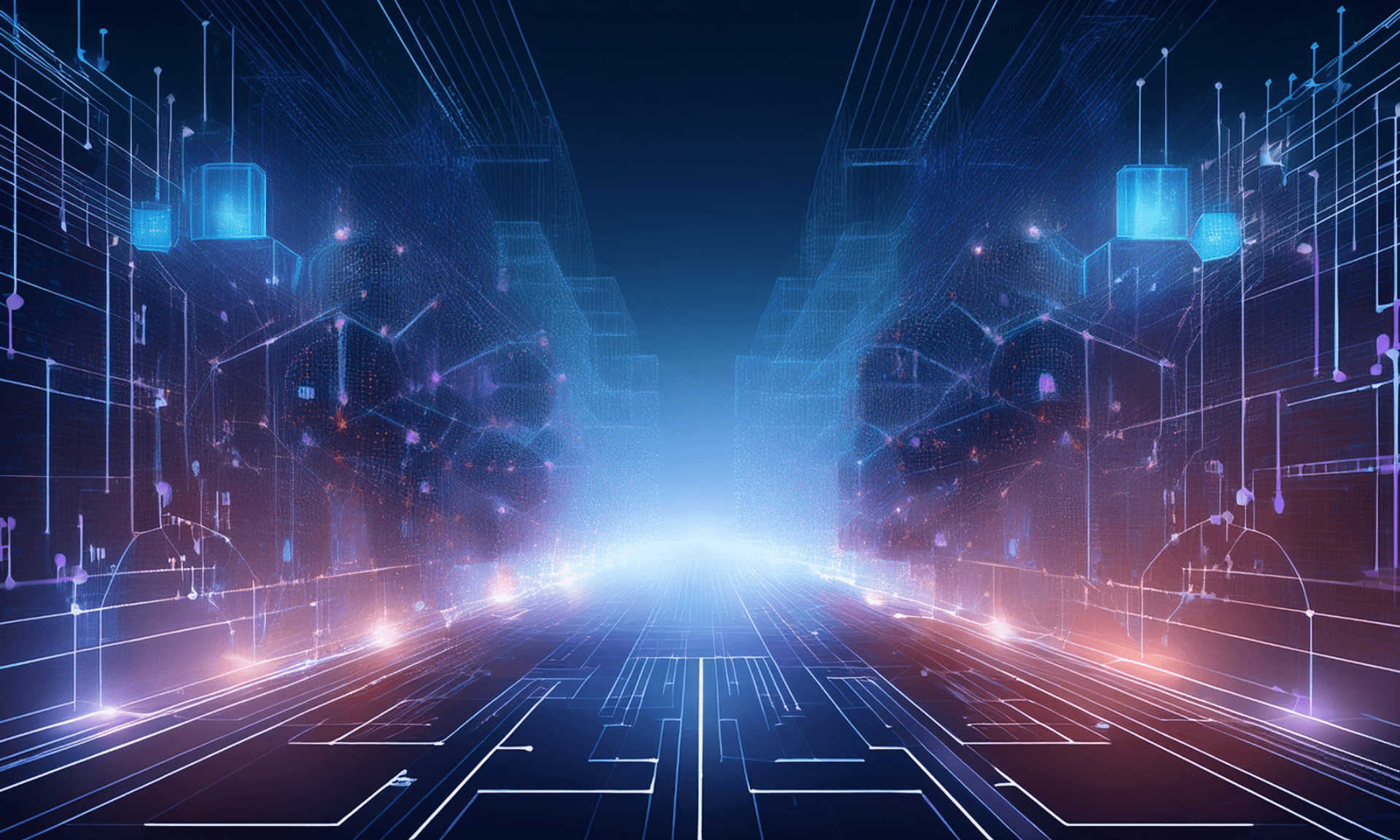
Lumenalta partners with CTOs and COOs to convert digital supply chain management objectives into measurable financial results. Our iterative engagement model aligns use-case sprints with cash flow targets, reducing time-to-value without increasing risk. Cross-functional architects integrate cloud-native analytics, zero-trust security, and compliance automation into a single operating fabric that scales across plants, partners, and geographies. This approach eliminates manual reconciliations, improves on-time performance, and yields hard savings that fund the next wave of modernization. Trusted collaboration, transparent metrics, and purpose-built accelerators maintain steady momentum for transformation from pilot to global rollout.
table-of-contents
- Why digital transformation in the supply chain matters now more than ever
- Understanding digital transformation across the extended supply chain
- How CTOs and COOs can address supply chain digital transformation challenges
- Key benefits of digital transformation in logistics and supply chain operations
- Common digital transformation challenges in supply chain management
- The current and future state of digital supply chain transformation
- How Lumenalta helps drive digital transformation supply chain management goals
- Common questions about digital transformation in logistics and supply chain
Common questions about digital transformation in logistics and supply chain
How can I justify the budget for digital transformation in the supply chain to my board?
What timeline should I expect for a full supply chain digital transformation?
Which data sources matter most for early wins?
How do I keep suppliers engaged during digital upgrades?
Can digital transformation reduce my carbon footprint without raising costs?
Want to learn how digital transformation can bring more transparency and trust to your operations?